Cut-resistant gloves are a type of personal protective equipment (PPE) used by anyone who works with sharp objects, machinery, or in environments where cuts and lacerations are common hazards. These gloves are specially engineered to protect the hands from injuries caused by sharp objects, such as blades, glass, and metal, which can lead to severe wounds or even the loss of fingers if not properly protected.
The European Commission has reported that in 2020, the most common non-fatal injuries in the workplace were wounds (followed by dislocations, concussions, and fractures), and while this data highlights the need for proper hand protection against cuts, we know that choosing the right cut protection gloves can be challenging – especially given the variety of materials, specifications, safety gloves suppliers, and cut levels to keep into account.
So, if you’re grappling with the challenge of selecting the ideal gloves for your use cases, this guide will offer you valuable insights into the factors to consider and the options available, ensuring that you make an informed and confident choice.
Here are the topics we will cover:
- What Are Cut-resistant Gloves Made Of?
- What Are The Levels Of Cut Resistance?
- How Do You Read Glove Cut Ratings?
- How To Select The Right Model?
- Care, Maintenance, And Disposal
- Limitations And Misconceptions
What Are Cut-resistant Gloves Made Of?
Cut-resistant gloves are manufactured using a variety of materials, each with its unique properties and advantages, making them suited for different applications.
Here’s a breakdown of some of the most common materials:
- Steel Core: This material is both cut and abrasion-resistant, making it a sturdy option for heavy-duty tasks.
- Metal Mesh: Made from stainless steel, metal mesh gloves are not only cut-resistant but also offer protection against punctures. They’re often used in food processing industries where there’s a high risk of hand injuries.
- Fibre-Metal Blends: These gloves are a combination of fibres and metals, making them both durable and cut-resistant. They offer a good balance between flexibility and protection.
- Kevlar Aramid Fiber: Renowned for its flexibility and lightweight nature, Kevlar is a material that’s five times stronger than steel. It’s also flame-resistant up to 427°C, making it suitable for applications involving heat.
- Spectra Fiber: Notable for its flexibility and ability to resist cuts and abrasions even when wet, Spectra is a material that’s 10 times stronger than steel per unit weight.
- Dyneema: Unique for its ability to float on water, Dyneema is also durable, moisture-resistant, and chemically resistant. It’s an impressive 15 times stronger than steel, making it suitable for various applications.
- Super Fabric: Known for its flexibility, Super Fabric offers resistance against punctures, cuts, and abrasions. It’s often used in industries requiring a high level of hand protection.
As you can see, each material offers distinct properties that cater to different requirements, such as cut resistance, flexibility, or chemical resistance. Being well-versed in the attributes of these materials empowers you to make an informed decision when choosing the perfect cut protection gloves tailored to your unique needs.
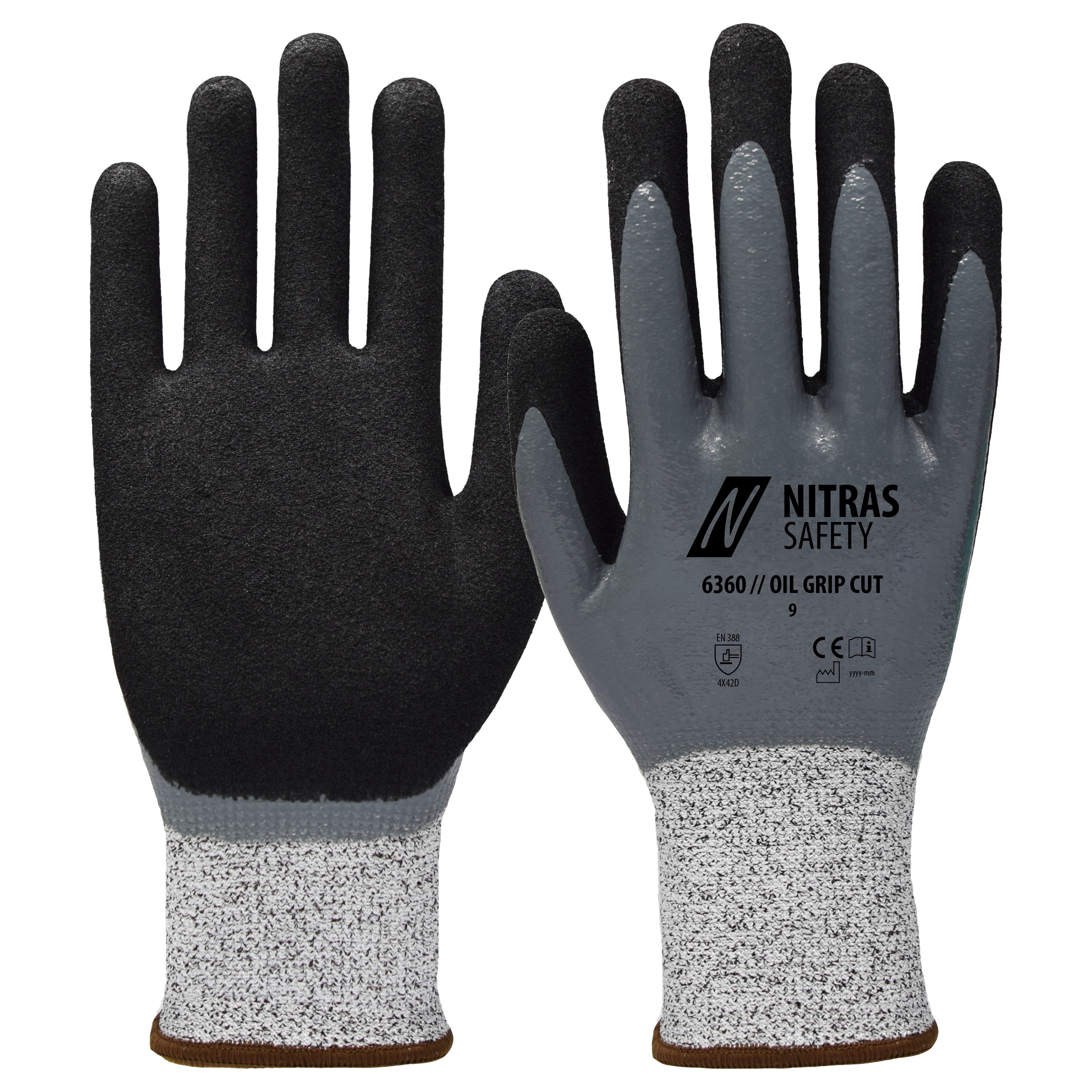


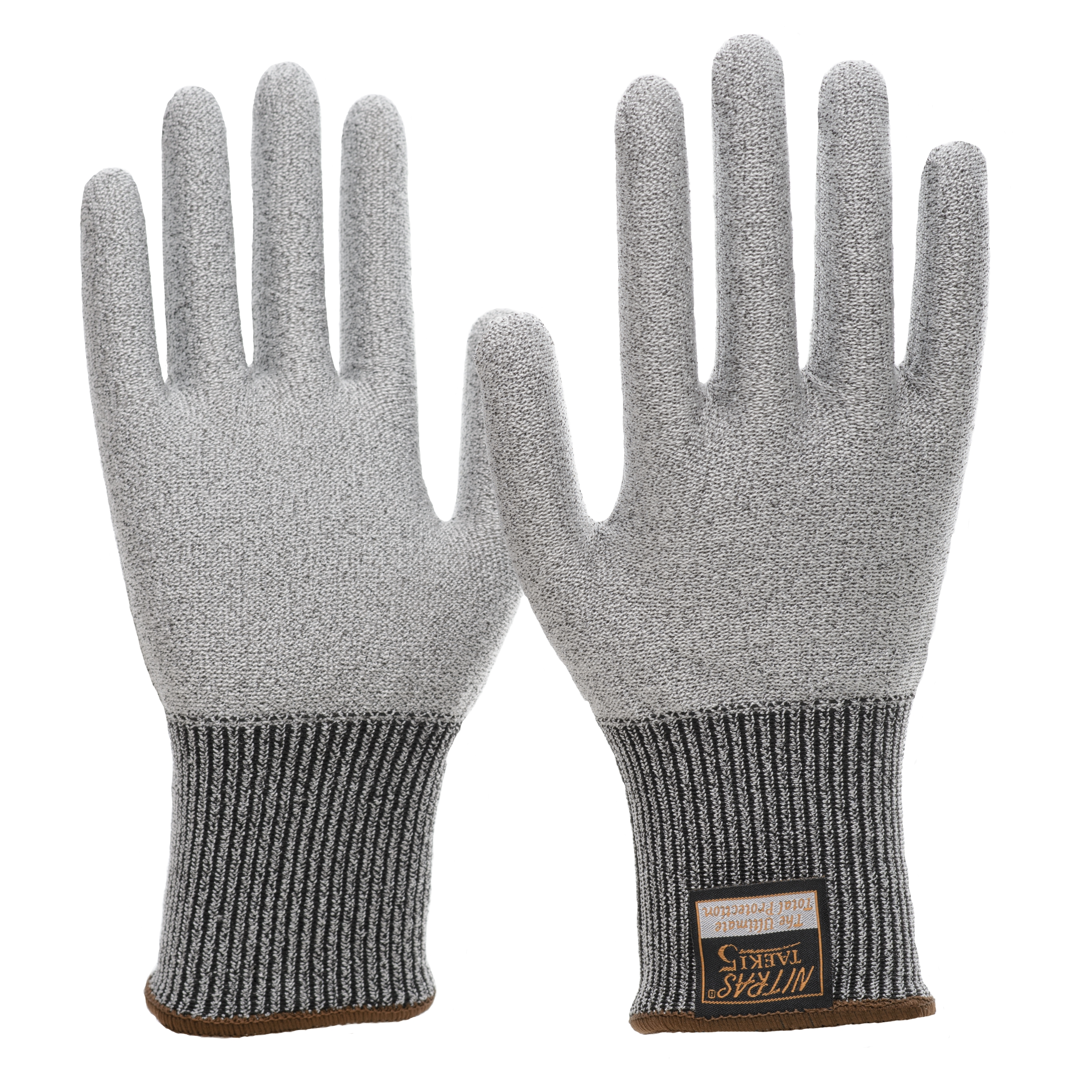

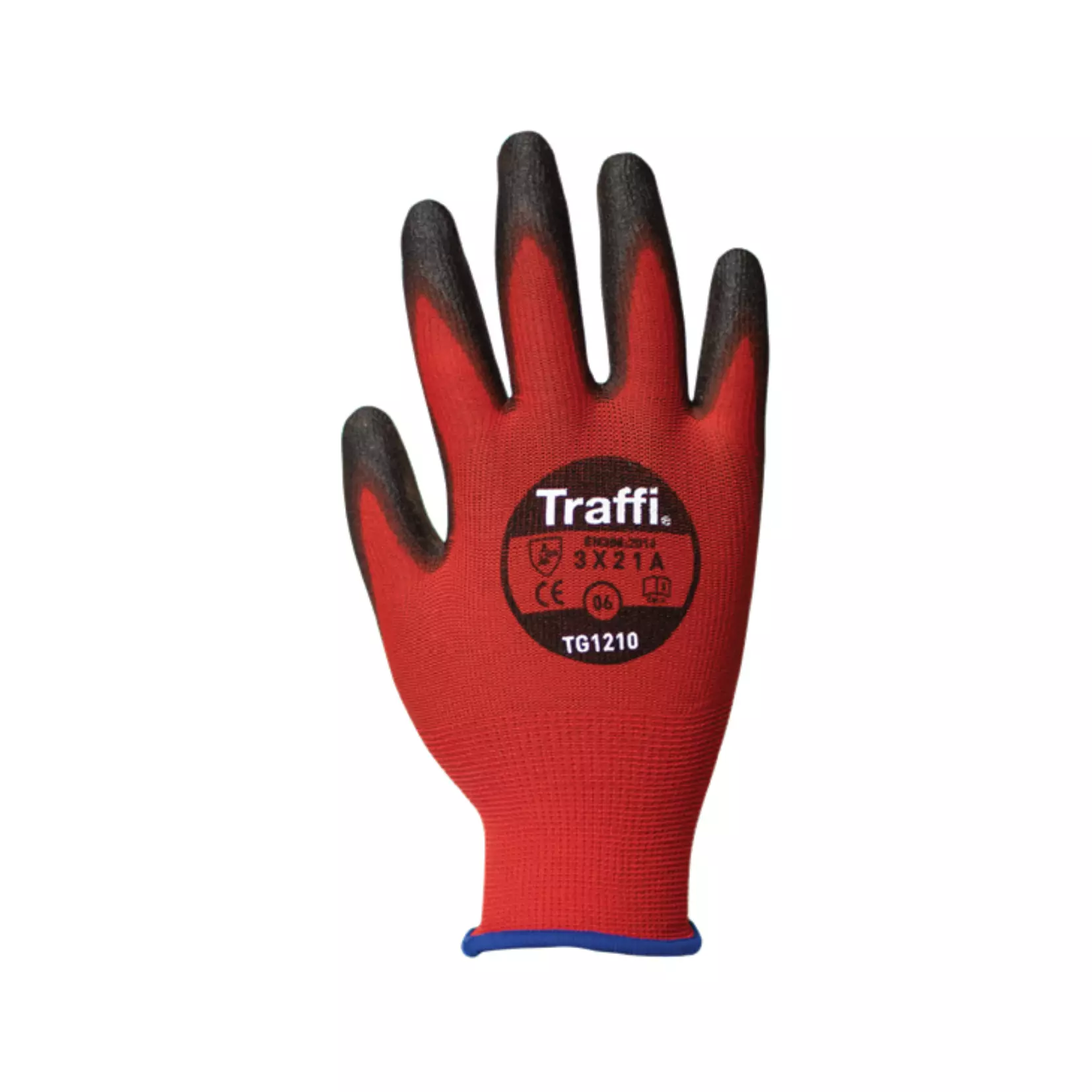
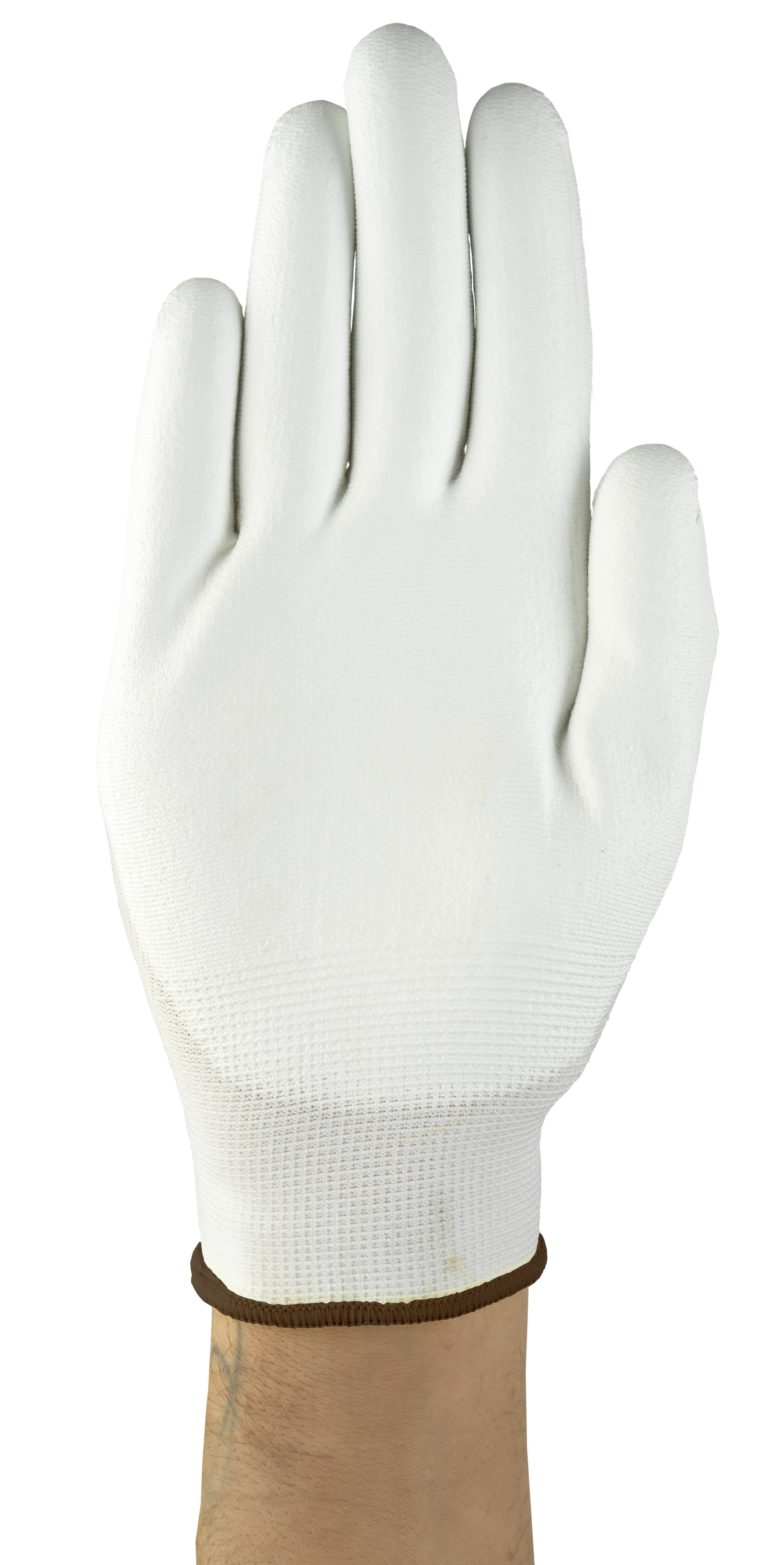
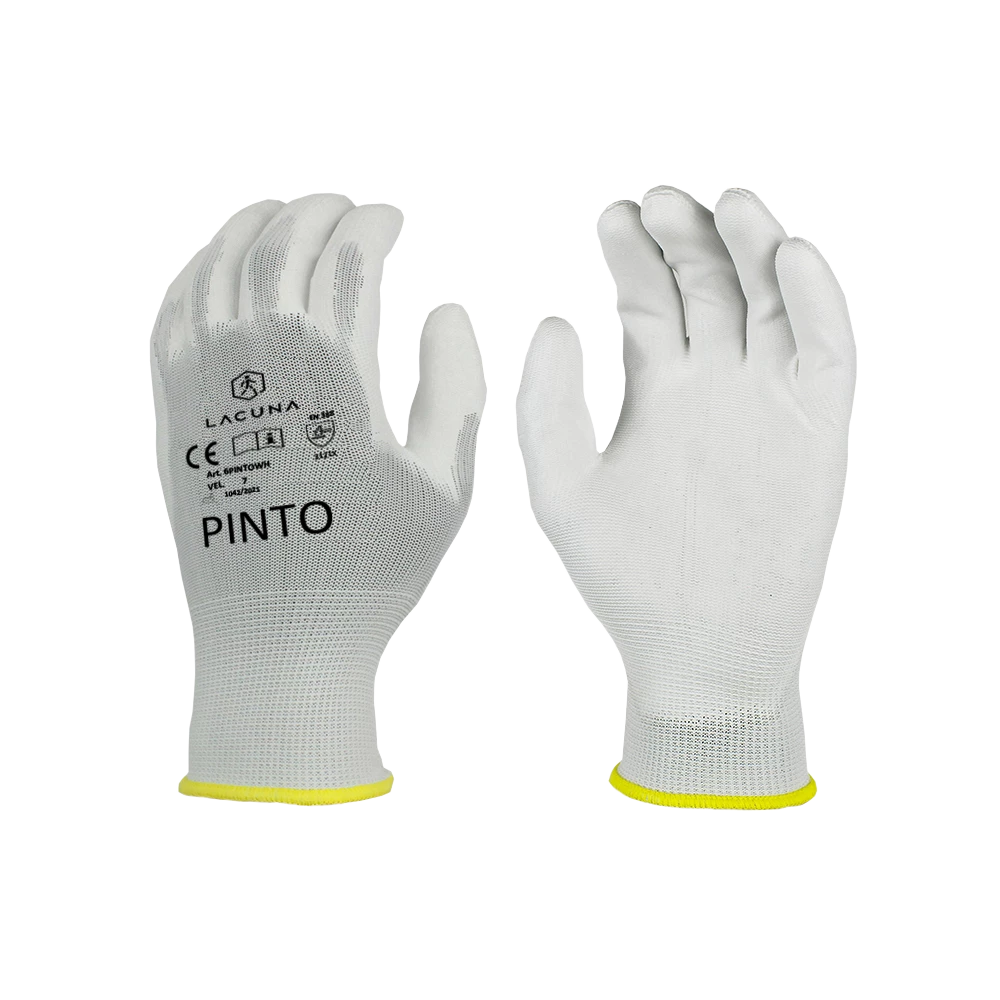
What Are The Levels Of Cut Resistance?
In Europe, the EN388 standard serves as the testing criterion for safety gloves against cuts, tears, punctures, and abrasions. This standard encompasses two distinct tests to assess cut resistance.
The initial test, known as the coupe test, evaluates a glove’s resistance to a circular blade and assigns a rating from 1 to 5, with higher scores indicating better resistance. With the 2016 revision of the EN388 standard, a new test was introduced—the ISO 13997 cut test, also referred to as the TDM test. This test measures a glove’s resistance to a straight-edged blade.
For the ISO 13997 test, a straight blade moves across a glove material sample at a consistent speed but with increasing force (measured in Newtons – N) until it penetrates the material. The glove’s cut resistance is then graded from A to F, with higher letters signifying better resistance. Specifically, level A (comparable to a 1–2 score in the Coupe test) signifies a 2N to 5N force is needed to cut through the material, while level F (equivalent to a score of 5 in the Coupe test) represents a force exceeding 30N.
Here’s a simplified chart of the levels of cut resistance:
Coupe Test Rating (1-5) | → | ISO 13997 Rating (A-F) |
1-2 | → | A (Force: 2N – 5N) |
3-4 | → | B (Force: 5N – 10N) |
4-5 | → | C (Force: 10N – 15N) |
4-5 | → | D (Force: 15N – 22N) |
4-5 | → | E (Force: 22N – 30N) |
5 | → | F (Force: >30N) |
Please note that the coupe test and the ISO 13997 test provide different measures of cut resistance, with the latter giving a more comprehensive assessment.
As a last note, here is a list of common activities for each cut protection class. Please notice, these are general guidelines, for more detailed information on the best cut protection class for your use cases, get in touch with our product experts.
- Typical tasks for Cut Protection Class E-F (activities with a high risk of skin punctures and cuts):
- Heavy construction
- Fixing works – Rescue operations
- Mining
- Iron processing
- Typical tasks for Cut Protection Class C-E (medium-risk tasks with a need for finger dexterity):
- Recycling tasks
- Landfills
- Electrical works
- Home maintenance tasks
- Typical tasks for Cut Protection Class A-B (low-risk tasks where any potential wounds would only be minor):
- Glass processing
- Catering and food industry works
- Small electrical works
- Small sheet metal works
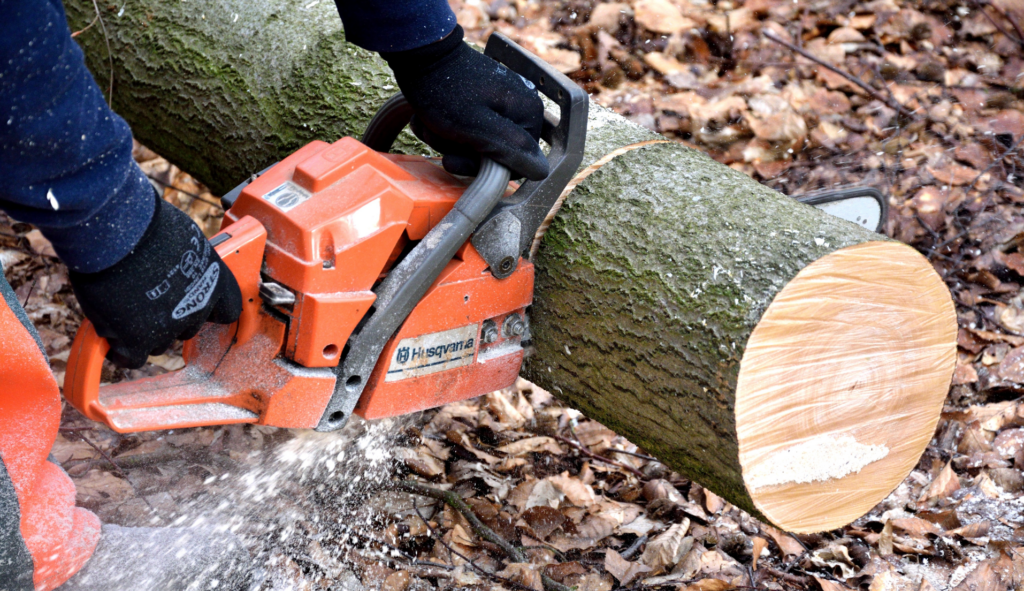
Safety gloves for cutting are manufactured using a variety of materials, each with its unique properties and advantages.
How Do You Read Glove Cut Ratings?
According to European product standards, all modern cut-resistant gloves must be classified with a sequence of 6 characters (including numbers and letters) which stand for the following:
- The first character indicates abrasion resistance: On a scale of 1-4, the more rounds of abrasive paper disc the glove can withstand, the higher the number.
- The second character stands for the old cut protection class: In the past, the second character indicated the rate of cut resistance on a scale of 1-5, based on the minimum number of passes with a circular blade needed to cut through the material. However, as this test has become less common due to a shift away from the former measurement technique, an ‘X’ is now frequently found in its place.
- The third sign indicates tear resistance: This rate is measured on a scale of 1-4 for the force required to tear the material. Please notice, that the highest grade does not necessarily guarantee the best level of cut protection.
- The fourth sign indicates puncture resistance: This rate is measured on a scale of 1-4. However, this number does not tell if the glove protects against small and very sharp objects such as needles.
- The fifth sign indicates the cut protection class: As mentioned in the previous section, cut resistance is now evaluated on a scale from A to F, with F representing the highest level of protection—resistance to a cut exerting a force of 30 Newtons or 30 kilograms.
- The sixth sign indicates impact resistance: The presence of this last character only depends on whether the glove passes the impact resistance test or not. If the glove does pass, it gets a ‘P’ as its final grade. If the test isn’t done or the glove doesn’t pass, then, no mark is given.
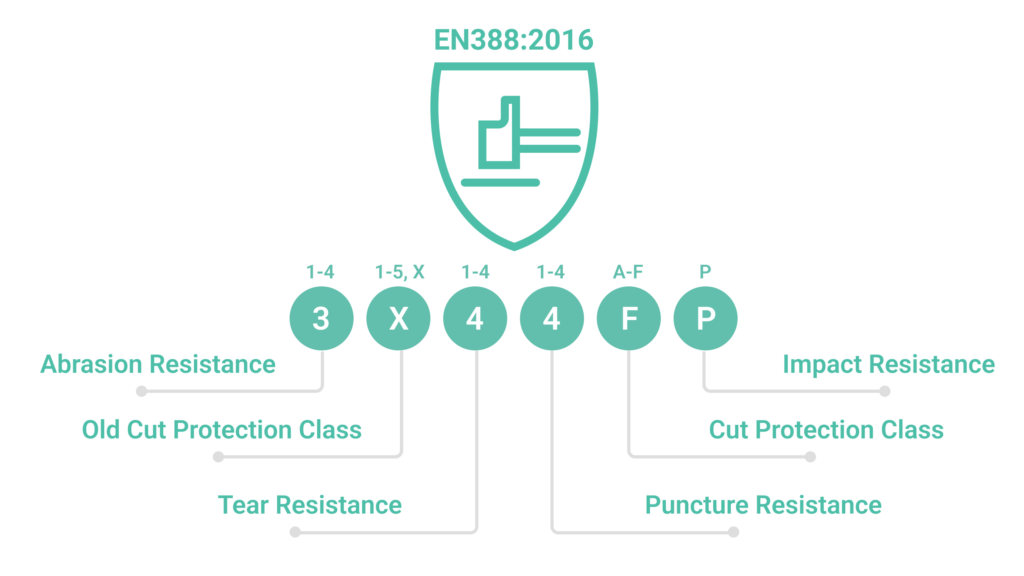
How To Select The Right Model?
Understanding the diverse use cases for cut protection gloves helps in choosing the appropriate level of protection for the intended task.
Here are some use cases with their relevant industries and levels of cut resistance:
- Food Processing: In this industry, workers often use knives and other sharp tools. Gloves for cutting food need to offer a good balance of cut resistance and dexterity. Typically, gloves with a cut rating of A or B (EN388) are suitable for these tasks.
- Glass Handling and Manufacturing: Workers in this industry handle sharp-edged glass sheets, requiring gloves with high cut resistance. Gloves with a cut rating of C or D (EN388) are generally recommended.
- Automotive Industry: Mechanics and other workers deal with sharp metal parts and tools. Gloves with a cut rating of B or C (EN388) offer the right balance of cut resistance and flexibility.
- Metal Fabrication: Metalworkers are exposed to sharp edges and heavy machinery. They need gloves with high cut resistance, usually in the D or E range (EN388).
- Construction: Construction workers use a variety of tools and face the risk of hand injuries. Gloves with a cut rating of C or D (EN388) provide sufficient protection.
- Medical Industry: Medical professionals use scalpels and other sharp instruments. Cut protection gloves with a rating of A or B (EN388) are suitable for most medical tasks.
- Butchery: Butchers work with sharp knives and bone saws, requiring gloves with high cut resistance. Gloves with a cut rating of D or E (EN388) are typically recommended.
- Forestry and Logging: Workers in this industry handle chainsaws and sharp tools, needing gloves with very high cut resistance. Chainmail gloves or gloves with a cut rating of E or F (EN388) are usually recommended.
- Fishing Industry: Fishermen deal with sharp hooks and tools, often in wet conditions. Gloves with a cut rating of C or D (EN388), made from materials like Dyneema that retain their cut resistance when wet, are ideal.
Please notice that these are general guidelines that might not apply to your specific settings and use cases. If you have doubts about what could be the best cut-resistant gloves for your business, we warmly recommend getting in touch with our experts for a personal consultation.
Care, Maintenance, And Disposal
As with all other Personal Protective Equipment (PPE), proper care and maintenance of your gloves will help you prolong their lifespan and maintain their protective properties.
These are general but effective practices to follow in order to ensure that your gloves remain effective and safe to use longer:
- Cleaning: Regularly clean your gloves according to the manufacturer’s instructions. Most gloves can be machine washed and air-dried. Ensure that you remove any contaminants, like oil or grease, from the gloves, as they can affect the performance.
- Inspection: Before each use, inspect your gloves for signs of wear, such as tears, cuts, or abrasions. If you notice any damage, replace the gloves immediately. Do not attempt to repair damaged gloves, as this could compromise their protective qualities.
- Proper Storage: Store your gloves in a cool, dry place, away from direct sunlight and chemicals. Proper storage helps prevent the degradation of the materials and ensures that the gloves are ready for use when needed.
- Use Appropriate Gloves: Ensure that you are using the right gloves for the task at hand. Consult the cut-level gloves chart and glove cut rating to select gloves with the appropriate level of protection for your specific needs.
- Rotate Your Gloves: If you gloves frequently, it’s a good idea to have multiple pairs and rotate their use. This practice not only prolongs the lifespan of each pair but also ensures that you always have a fresh pair ready for use.
- Disposal: When it’s time to dispose of your gloves, follow your local waste disposal regulations. If the gloves are contaminated with hazardous materials, they may need to be disposed of as hazardous waste. Also, consider recycling options, as some materials like Dyneema and Kevlar are recyclable.
- Replacement: Even the best cut-resistant gloves on the market are not a one-time investment. Over time, even the best models will wear out and need to be replaced. When you notice signs of wear or a decrease in performance, it’s time to invest in a new pair.
Limitations And Misconceptions
Here are some of the most common myths and misconceptions about cut-resistance gloves. We warmly invite you to read this list:
- “They are 100% Cut-Proof”: The reality is that no glove is truly “cut-proof.” Due to their inherent need for flexibility, dexterity, and ease of donning and removal, gloves cannot be impenetrable. While they may resist cutting, they can still be cut with determined effort or specialized tools—even chainmail gloves. Cut protection gloves, however, do significantly reduce the chances of sustaining a cut, and even when a cut does occur, the severity of the injury is often drastically minimized.
- “Cut Resistance Diminishes After Washing”: It’s a myth that the protective properties of safety gloves for cutting degrade after a few washes. In fact, washing can actually make the glove structure denser, enhancing mechanical and protective properties. Degradation in cut resistance typically occurs after varying periods of usage, not a few washes. But, do be aware that gloves made from weaker fibres may not last as long and always check the manufacturer’s guidelines.
- “Leather is Cut-Resistant”: While leather is durable, it is merely tanned skin, and skin is not cut-resistant. Leather gloves can offer significant cut protection, but only when they are reinforced with a liner made from materials like Kevlar or Dyneema.
- “They Lack Grip and Dexterity”: There’s a misconception that cut-resistant gloves do not offer adequate grip or dexterity. The truth is that they have evolved to provide wearers with both comfort and flexibility. Modern cut protection gloves typically feature textured finishes on the fingertips and palms for enhanced grip. Their construction with thin and flexible fibres also allows for easy hand movements while still providing robust protection against severe injuries.
- “Higher Cut Level Means Better Protection”: While it might be tempting to think that gloves with higher cut-resistance levels offer better protection, it’s not necessarily true. The cut-resistance level is an indication of protection against specific hazards, not a measure of overall resistance strength.
- “They Are Only for Heavy-Duty Jobs”: Cut-resistant gloves are not exclusive to heavy-duty tasks. They are widely used across various work environments, with protection levels tailored to specific occupational needs. That’s why, when selecting gloves, you should always consider their protective properties in the context of the specific job tasks and hazards, rather than focusing solely on the resistance rating.
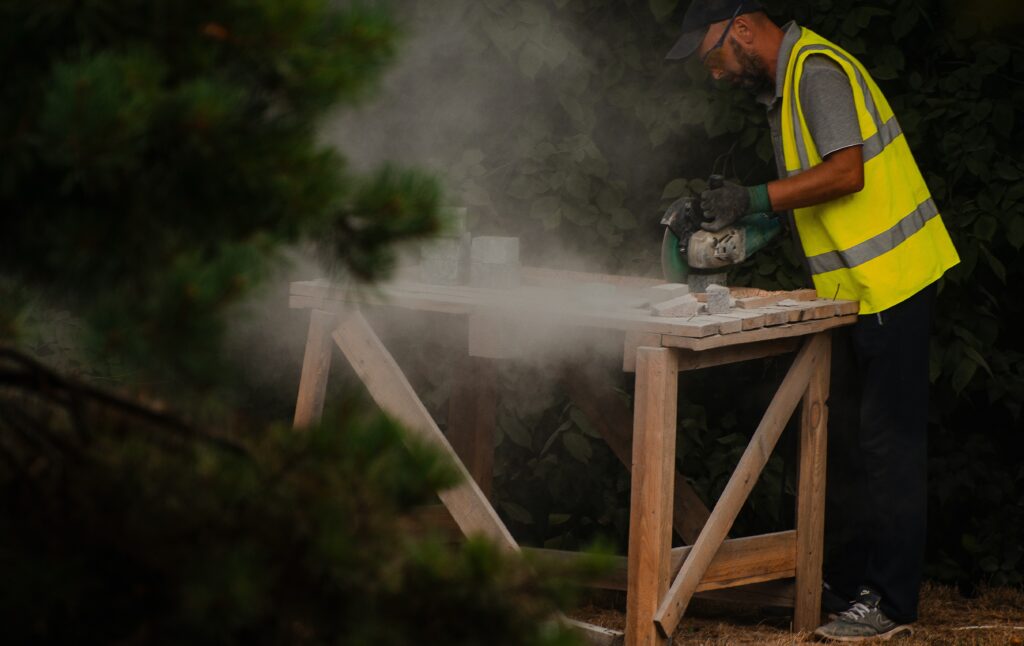
Conclusion
Selecting the best cut protection gloves for your settings is a decision that requires an in-depth understanding of your specific working conditions, tasks, and the risks involved.
The materials used in these gloves, such as Kevlar, Dyneema, and steel core, offer unique benefits, ranging from exceptional cut resistance to high durability and flexibility – the EN388 standard provides essential information on cut resistance levels, helping you make an informed choice.
It’s important to note that even high-rated gloves are not 100% cut-proof, and proper care and maintenance are necessary to prolong for their effectiveness. Regular inspection, cleaning, and correct storage are also key to ensuring the longevity and performance of your gloves.
Next, you can check our complete selection of cut-resistant gloves sourced from vetted European suppliers, or get in touch with our experts for a free consultation.