The EN 13034 standard is a key regulation in the world of personal protective equipment (PPE). It defines the requirements for protective clothing against liquid chemicals, specifically offering protection for professionals who face occasional exposure to chemical splashes. This standard helps employers and safety managers choose the right gear for their teams and ensures that workers have the appropriate level of safety. In this article, we’ll break down what EN 13034 covers, who it applies to, and why it’s crucial for maintaining workplace safety.
Resistance to Penetration by Liquids Explained
The EN 13034 standard assesses protective clothing’s resistance to chemical penetration using the EN ISO 6530 test method. In this test, fabric samples are exposed to specific chemical liquids under controlled conditions to measure penetration and repellency. The chemicals tested include sulfuric acid (30%), sodium hydroxide (10%), o-xylene, and butan-1-ol. The results are measured in terms of penetration and repellency percentages, rated on a scale from 1 to 3. A higher rating indicates better resistance to penetration and higher repellency, ensuring more effective protection for workers facing occasional chemical splashes.
Abrasion Resistance Explained
The EN 13034 standard measures the abrasion resistance of protective clothing using the EN 530 test method, specifically Method 2. In this test, fabric samples are subjected to abrasion using a Martindale abrasion tester, which simulates wear and tear. The results are rated on a scale from 1 to 6 based on the number of abrasion cycles the fabric can withstand before showing signs of damage. A higher rating indicates better resistance to abrasion, ensuring the protective clothing remains effective even in challenging working conditions.
Tear Resistance Explained
The EN 13034 standard requires protective clothing to meet specific tear resistance levels to ensure durability and safety. Tear resistance is assessed using the EN ISO 9073-4 test method. In this procedure, fabric samples are subjected to increasing force until they tear, simulating the stresses encountered in the workplace. The results are measured in Newtons (N) and rated from 1 to 6, with a higher rating indicating stronger tear resistance. Meeting the tear resistance requirements ensures that the protective clothing can withstand the rigors of everyday use, providing reliable protection against occasional chemical splashes.
Tensile Strength Explained
In the context of the EN 13034 standard, tensile strength is a crucial measure of a fabric’s durability and reliability. The standard requires protective clothing to meet specific tensile strength levels, ensuring that the material can withstand the stresses of daily use. Using the EN ISO 13934-1 test method, fabric samples are stretched until they break to determine their maximum tensile strength. Results are measured in Newtons (N) and rated from 1 to 6, with higher ratings indicating stronger and more durable fabric. Meeting the tensile strength requirements ensures that protective clothing remains intact and effective in providing protection against occasional chemical splashes.
Puncture Resistance Explained
The EN 13034 standard includes specific requirements for puncture resistance to ensure protective clothing can withstand sharp objects that might compromise its integrity. Puncture resistance is tested using the EN 863 method, where a standard-sized steel stylus is forced through fabric samples under controlled conditions. The force required to penetrate the material is measured in Newtons (N) and rated from 1 to 6, with higher ratings indicating better puncture resistance. Meeting these puncture resistance requirements ensures that the protective clothing offers reliable defense against accidental splashes of liquid chemicals, even in environments where sharp tools or debris are present.
Antistatic Properties Explained
Under the EN 13034 standard, protective clothing is required to have antistatic properties to minimize the risk of static-related accidents in environments where flammable chemicals are present. This is measured using the EN 1149-5 test method, which ensures that the fabric dissipates electrostatic charges efficiently. The clothing must meet specific surface resistance or charge decay requirements to qualify. Proper antistatic properties reduce the risk of sparks that could ignite volatile substances, providing an additional layer of safety for professionals exposed to occasional chemical splashes in potentially explosive atmospheres.
Limited Flame Spread Explained
Under the EN 13034 standard, limited flame spread testing is an optional requirement aimed at ensuring additional safety in environments with potential flame exposure. The test, conducted according to EN ISO 14116, measures how well the fabric resists ignition and prevents the spread of flames. Fabric samples are exposed to a controlled flame, and their behavior is assessed based on after-flame time, after-glow time, and whether they produce flaming debris. Results are rated on a scale from 1 to 3, with a higher rating indicating better flame resistance. Although optional, meeting these requirements provides an extra layer of protection against occasional chemical splashes in workplaces where accidental exposure to fire could occur.
How to Read Markings of EN13034 Standard
To read the markings of the EN 13034 standard, look for specific symbols and numbers on the protective clothing label. The “EN 13034” marking indicates compliance with the standard for chemical protective clothing against liquid splashes. Next to this, you’ll see “Type 6,” denoting limited protection against light sprays or fine mists of chemicals. Alternatively, you might see “Type PB [6]” where “PB” stands for “Partial Body,” indicating that the garment is designed to cover only part of the body, like jackets or aprons.
Additional codes provide ratings for different performance criteria like abrasion resistance, tear resistance, and antistatic properties. For instance, “a/b/c/d” represents specific chemical penetration and repellency ratings. Understanding these markings helps you choose the right protective gear for your needs.
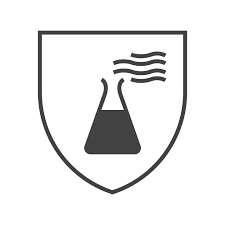
Marking | Meaning |
---|---|
Type 6 | Limited protection against light sprays or fine mists of liquid chemicals. |
Type PB [6] | “Partial Body” protection, covering only part of the body (e.g., jackets, aprons). |
a/b/c/d | Ratings for specific chemical penetration and repellency (e.g., sulfuric acid, sodium hydroxide). |
Antistatic Properties | Indicates compliance with antistatic requirements under EN 1149-5. |
Abrasion Resistance | Rated from 1 to 6 based on abrasion cycles, using the EN 530 standard. |
Tear Resistance | Rated from 1 to 6 based on resistance to tearing forces under EN ISO 9073-4. |
Tensile Strength | Rated from 1 to 6 based on tensile strength using the EN ISO 13934-1 standard. |
Puncture Resistance | Rated from 1 to 6 based on resistance to puncture forces under EN 863. |
Limited Flame Spread (Optional) | Indicates compliance with flame spread properties under EN ISO 14116 (optional test). |
Where Are Products with EN 13034 Standard Used?
Products with the EN 13034 standard are used in environments where workers face occasional exposure to chemical splashes. Lab technicians wear Type 6 coveralls in research facilities when handling mild chemicals. Maintenance workers use Type PB [6] aprons for partial body protection while cleaning machinery. Factory employees in chemical manufacturing wear these garments to protect against light chemical sprays. Agriculture workers apply pesticides while wearing them to shield themselves from fine mist. This standard ensures that workers in various industries have reliable protection against incidental chemical exposure.

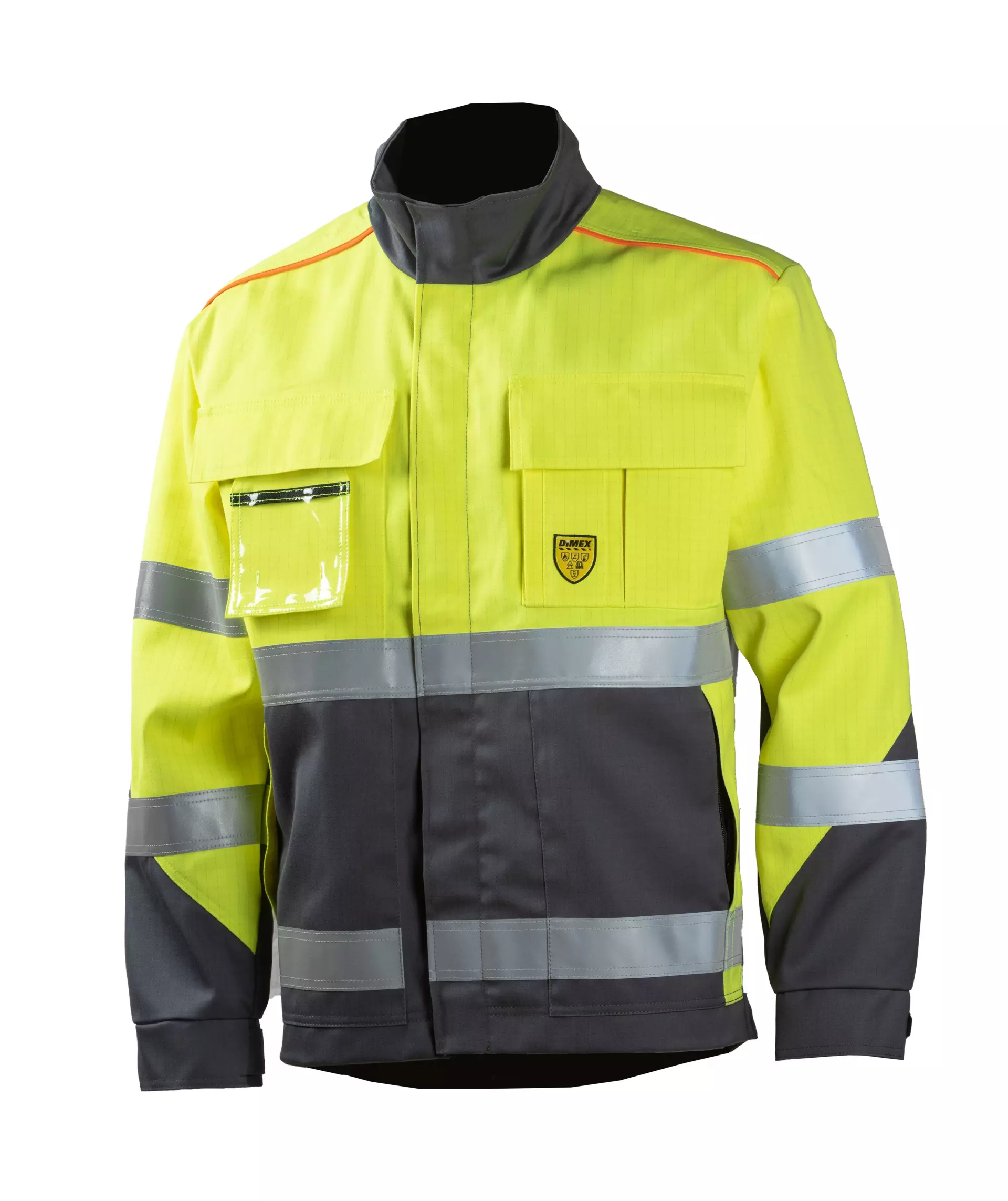
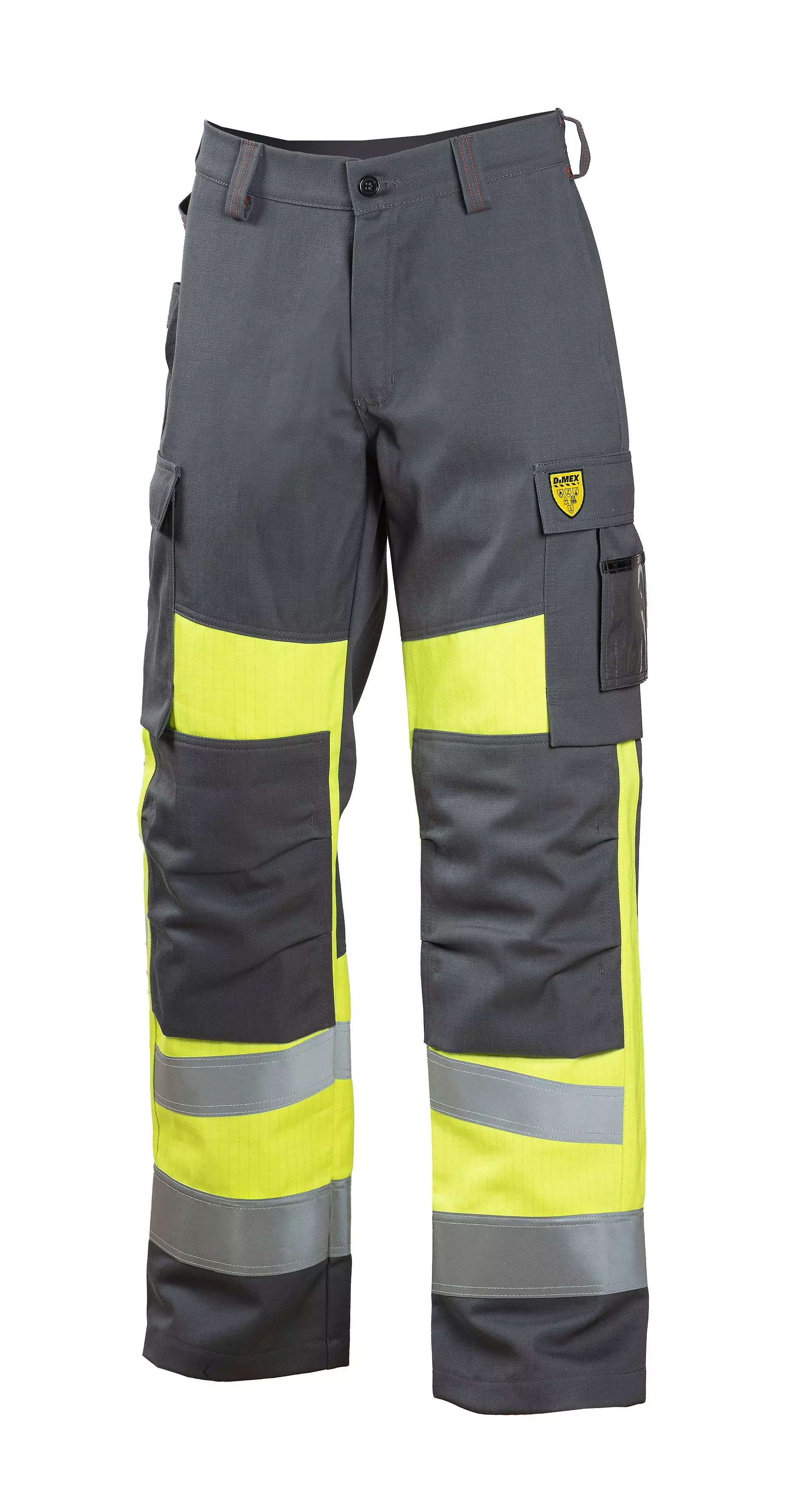
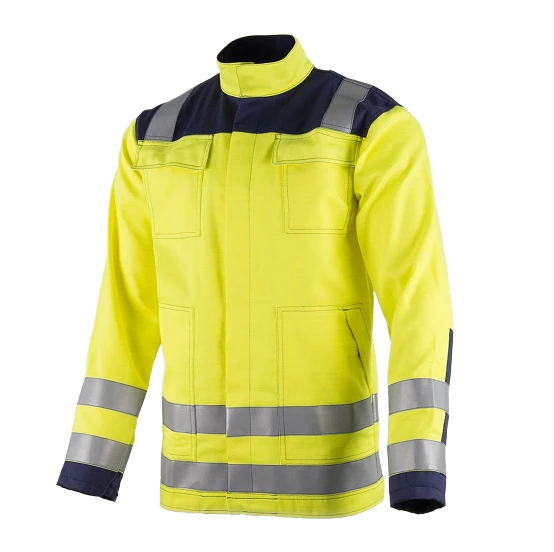

Conclusion
Understanding the EN 13034 standard is crucial for selecting the right protective clothing against occasional chemical splashes. The standard’s markings, such as Type 6 or Type PB [6], provide clear guidance on the level and type of protection offered. By knowing the meaning behind the ratings for penetration, abrasion, tear, tensile strength, puncture resistance, and antistatic properties, employers can make informed decisions. This ensures that workers across industries like laboratories, manufacturing, and agriculture remain safe and adequately protected.