With a well-executed Total Cost of Ownership (TCO) evaluation, procurement professionals can not only control costs effectively but also enhance their overall operational performance.
Total Cost of Ownership (TCO) encompasses a holistic assessment of every cost related to the ownership and operation of a specific asset or product over its lifetime. This includes not only the initial acquisition cost but also ongoing expenditures like maintenance, support, and training, as well as potential risks. A thorough identification and evaluation of these costs empower businesses to make well-informed decisions that can reduce expenditure and enhance operational efficiency.
If you want to read more on mastering Total Cost of Ownership for your procurement strategy, donât miss our previous article: Mastering TCO: The Essential Guide for Procurement Professionals
In this practical step-by-step guide, we will walk you through the actual process of calculating your TCO.
Here are the 6 steps you are about to read:
- Step 1: Define the scope and objectives
- Step 2: Identify cost categories
- Step 3: Gather data and quantify costs
- Step 4: Calculate the present value
- Step 5: Analyze and interpret the TCO data
- Step 6: Make informed decisions and implement cost-control strategies
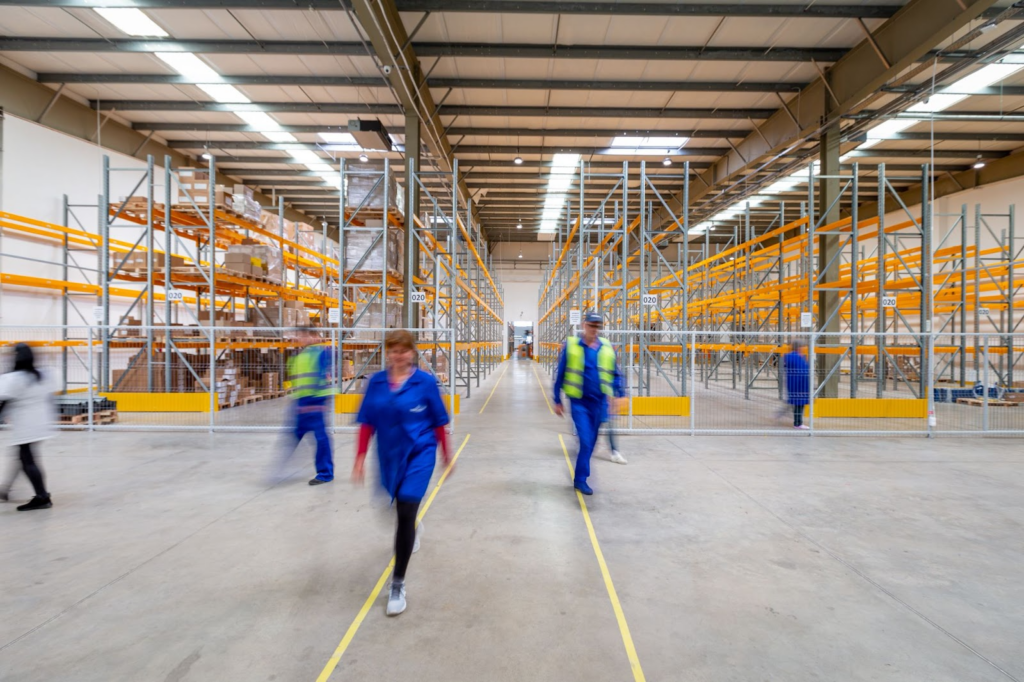
With a well-executed Total Cost of Ownership (TCO) evaluation, procurement professionals can not only control costs effectively but also enhance their overall operational performance.
Step 1: Define the Scope and Objectives
Before embarking on your Total Cost of Ownership (TCO) calculation, you must first define the scope and objectives of the analysis.
Determine the specific asset or product you want to evaluate and establish the purpose of the TCO assessment. Are you comparing different suppliers or assessing the viability of an in-house solution? Clarifying these aspects will help you focus your efforts and gather the necessary data for an accurate TCO evaluation.
Step 2: Identify cost categories
To calculate TCO comprehensively, it is essential to identify and categorize all the costs associated with the asset or product under consideration.
Some common cost categories include:
- Initial Purchase Costs: These include the upfront cost of acquiring the asset, such as the purchase price, installation expenses, and any customization or configuration fees.
- Operating Costs: These encompass ongoing expenses incurred during the asset’s lifecycle, such as maintenance, repairs, upgrades, consumables, and utilities.
- Training and Support Costs: Consider the costs associated with training personnel to use and maintain the asset effectively. Additionally, factor in any support services or warranties provided by the supplier.
- Downtime and Risk Costs: Assess the potential risks and downtime associated with the asset, including potential disruptions to operations, loss of productivity, and potential damages.

Step 3: Gather data and quantify costs
Once you have identified the cost categories, collect the relevant data to quantify the costs accurately.
This may involve consulting financial records, supplier agreements, maintenance logs, and other relevant sources of information. Ensure that you capture both direct costs (easily quantifiable) and indirect costs (challenging to quantify but equally important) to get a holistic view of the TCO.
As a reference, this is what we mean by direct and indirect costs:
- Direct costs: they are the figures that you initially notice on an invoice, primarily because they directly impact your immediate financial outlay. Examples include the purchase price of a product or equipment, shipping costs, and any installation or setup fees. Essentially, these costs have a clear and unambiguous connection to the product you are acquiring.
- Indirect costs: they may not be as easily discernible but are equally important in determining your TCO. Indirect costs are the expenses incurred during the life cycle of the product or service, which might not be directly tied to its purchase but are still integral to its operation and maintenance. Examples include storage costs, where you need space to house the product; maintenance costs, which are necessary to keep the product in working condition; training costs, incurred to ensure your staff can effectively use the product; and disposal costs, related to the eventual removal or replacement of the product. These costs, while not as immediately apparent as direct costs, can significantly contribute to the overall expenditure over time.
Step 4: Calculate the present value
Understanding that costs are not just one-time events, but rather they span over the life cycle of a product or service, it’s essential to calculate the present value of these future costs. This gives a clearer picture of their real impact on your present financial status.
The present value of future costs takes into consideration the current value of money that will be spent in the future. This process, known as discounting, accounts for inflation and the time value of money – the concept that a dollar today is worth more than a dollar in the future due to its earning potential.
To calculate the Total Cost of Ownership (TCO) in procurement, you would typically follow this simple formula:
I + M – R = TCO
- Initial cost (I): This is the purchase price or the amount you shell out to acquire the asset.
- Maintenance cost (M): This comprises the expenses incurred to maintain the asset’s functionality over the long haul.
- Residual cost (R): This is the anticipated value of the asset over an extended period, say, five years.
While it might sound a bit complex at first, plenty of financial models and TCO calculators are available to simplify this process, making it easy for beginners and ensuring accuracy in your calculations.
Step 5: Analyze and interpret the TCO data
Once you have quantified and discounted all relevant costs, it’s time to analyze the data and gain meaningful insights.
Consider the following factors during your analysis:
- Cost Comparison: Compare the TCO of different assets or products to determine which option offers the best value for money. Look for cost differentials across various cost categories and identify potential areas for cost savings.
- Lifecycle Considerations: Assess how costs fluctuate throughout the lifecycle of the asset. This will help you understand when significant expenses are likely to occur and plan accordingly.
- Sensitivity Analysis: Conduct sensitivity analysis to evaluate how changes in certain variables, such as inflation rates or maintenance costs, can impact the TCO. This analysis will help you assess the robustness of your calculations and identify potential risks.
- Risk Assessment: Evaluate the risks associated with each option and factor in the potential costs of mitigating those risks. This step is crucial in making informed decisions that minimize future liabilities.
Step 6: Make informed decisions and implement cost-control strategies
Armed with a thorough understanding of the TCO data and analysis, it’s time for you to start making informed decisions and implement effective cost-control strategies.
Consider the following approaches:
- Supplier Negotiations: Use the TCO analysis to negotiate favourable contracts with suppliers. The insights gained from the evaluation can provide leverage in negotiations and help secure more advantageous pricing and terms. On a related note, procurement professionals should always consider the tangible advantages of expanding their supplier base. A larger pool of suppliers presents an opportunity for you to compare and select the best volume deals on your go-to supplies, and this is where a marketplace like Droppe can tip the scale in favour of your TCO. On Droppe you can compare the catalogues and purchase from a pool of 100+ trusted European suppliers all in one consolidated invoice. This streamlined approach will simplify your procurement process, potentially reducing administrative costs, which are a critical indirect factor in the TCO.
- Process Improvements: Identify areas where process improvements can lead to cost savings. For example, optimizing maintenance schedules or implementing energy-efficient practices can help reduce operating costs.
- Asset Lifecycle Management: Utilize the TCO analysis to develop a comprehensive asset lifecycle management strategy. This strategy should include maintenance plans, asset replacements or upgrades, and monitoring to ensure ongoing cost control.
To calculate the Total Cost of Ownership (TCO) in procurement, you would typically follow this simple formula: I + M – R = TCO
Conclusion
By understanding and leveraging the Total Cost of Ownership (TCO) concept, businesses can make well-informed decisions that drive cost control and operational efficiency.
Calculating TCO involves defining the scope, identifying cost categories, quantifying costs, discounting future expenses, analyzing data, and implementing cost control strategies.
With a comprehensive TCO evaluation, businesses can optimize procurement decisions, negotiate better contracts, and drive long-term cost savings.
Take advantage of TCO analysis to gain a competitive edge and unlock greater value from your procurement processes.
Remember, TCO is not a one-time calculation but an ongoing process that requires periodic reassessment. Regularly review and update your TCO analysis to adapt to changing market conditions, technologies, and business needs. By prioritizing TCO evaluation as an integral part of your cost analysis and control strategy, you can enhance your organization’s financial performance and achieve sustainable growth.
