Choosing the right face shield for welding is key to ensuring comfort and safety while you work. With so many options available, it can be hard to know what to look for. In this guide, we’ll walk you through the essential factors like material, optical clarity, comfort, and safety standards, so you can easily find the perfect shield for your needs.
By the end of this article, you’ll have all the information to make a confident choice. We’ve covered everything you need to know to make sure you’re well-equipped for your tasks.
We’ll also provide tips on maintaining your shield and introduce related products, ensuring you have the best possible protection for your work. Ready to find your ideal face shield and solve any other safety concerns you might have? Let’s dive in!
For a broader perspective, explore our main guide “How To Choose The Right Face Shields – A Buyer’s Guide”.
Key Factors to Consider When Selecting Welding Face Shields
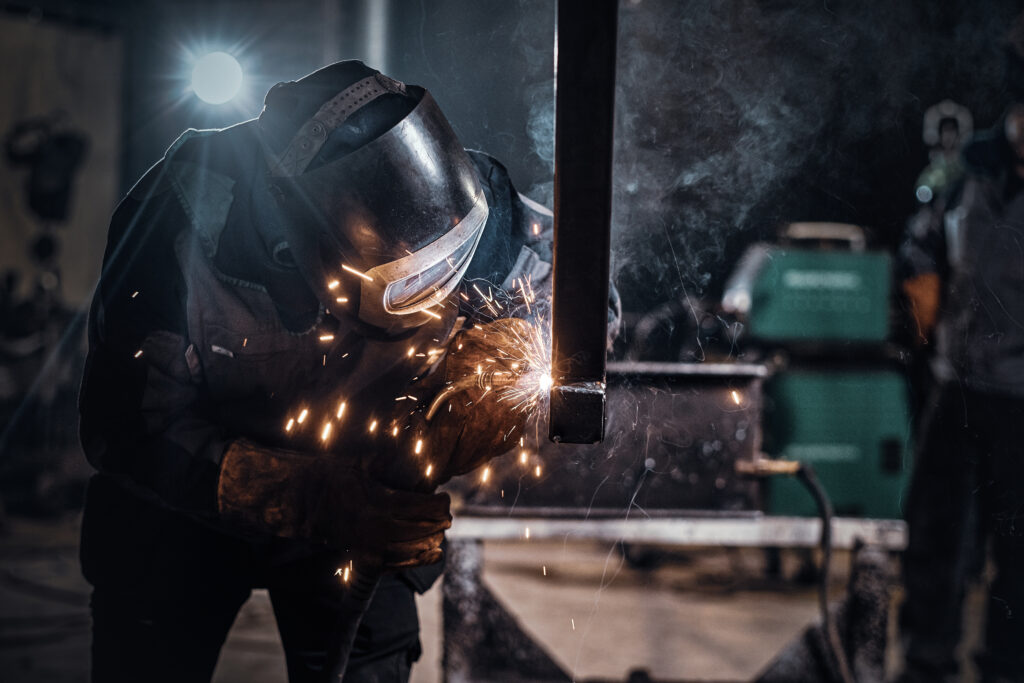
1. Material and Durability
The material of your face shield directly affects its durability and resistance to impacts or heat. Polycarbonate shields are widely preferred due to their excellent resistance to high temperatures and impact. For welding, ensure the shield is also rated for thermal stability.
- Polycarbonate: Heat and impact-resistant; ideal for welding.
- Nylon: Lightweight and flexible, often used in headgear.
- Metal: Used in specific shield designs for extreme durability.
Check for compliance with EN 166 and ISO 12312-1 standards for protective eyewear. Adding a brief explanation of these standards and linking to authoritative resources could increase clarity.
2. Optical Clarity and Shade Levels
Welding produces intense UV and IR radiation. Ensure the shield meets European shade standards (DIN EN 169). These standards specify the levels of protection required against UV and IR radiation, crucial for safeguarding your eyes during welding. For example, lower shade levels are suitable for light tasks like soldering, while higher levels are essential for arc welding. Refer to the table above to determine the appropriate shade level for your task. Look for models with adjustable shade levels to suit different welding types, such as MIG, TIG, or arc welding. Modern auto-darkening helmets are particularly useful, as they adapt to varying light conditions.
Welding Type | Recommended Shade Level |
MIG | 10-13 |
TIG | 9-12 |
Arc | 8-13 |
Provide a quick guide or decision flowchart to help readers match welding tasks with appropriate shade levels.
3. Comfort and Fit
A well-fitting face shield enhances comfort and helps you maintain focus during your work. Look for adjustable headgear with padded straps and lightweight construction. Ergonomic designs distribute weight evenly to reduce neck strain.
Illustrate examples of ergonomic designs with pros and cons to assist in decision-making.
Safety Standards and Certifications
In Europe, face shields must adhere to stringent safety standards. When selecting a shield, ensure it complies with:
- EN 166: General protection against impact and penetration.
- EN 169: Standards for welding filters and protection against radiation.
- CE Marking: Indicates conformity with EU safety standards.
Learn more about EN Standards from this guide in Wikipedia.
Specialized Features to Look For
1. Auto-Darkening Technology
Auto-darkening helmets automatically adjust the lens’s shade level based on the intensity of the welding arc. For example, models like the XYZ100 feature a fast response time of 1/25,000 seconds and adjustable sensitivity settings, while the ABC200 offers a wider shade range and grind mode. Here’s a comparison of key models:
Model | Response Time | Shade Range | Special Features |
Ardon Safety E1273 Climax | 1/25,000 seconds | 9-13 | Adjustable sensitivity |
JSP AFF122-440-408 AFP-25 | 1/30,000 seconds | 5-13 | Grind mode, wider range |
Bolle Safety FLASHV | 1/20,000 seconds | 8-14 | Enhanced comfort padding |
This comparison can help you decide which model suits your specific welding needs. This feature improves both safety and efficiency, as it reduces the need to manually adjust the shield.
2. Anti-Fog and Anti-Scratch Coatings
Anti-fog and anti-scratch coatings enhance clarity and ensure uninterrupted visibility even during demanding conditions. Opt for shields with anti-fog and anti-scratch coatings for clear vision.
3. Ventilation
Good ventilation promotes comfort and sustained productivity during long welding sessions by reducing heat buildup. Look for models with integrated airflow systems.
Expand this section by detailing how ventilation impacts safety and comparing common systems.
Comparing Face Shields and Related PPE
Welding tasks often require additional protection beyond face shields. Consider pairing your shield with:
- Safety Glasses: For added protection against flying debris. Learn more in “How To Choose Safety Glasses – A Buyer’s Guide”.
- Welding Helmets: For full-face and head protection. Read “Welding Helmets: Everything You Need To Know”.
Explore related product categories like “Safety Glasses” for comprehensive safety solutions. Including a visual comparison table or graphic showcasing key differences between these PPE types could be very useful.
Maintenance Tips for Prolonged Use
A well-maintained face shield lasts longer and performs better. Follow these tips:
- Regular Cleaning: Use a mild soap solution and a soft cloth to clean the visor.
- Inspect for Damage: Regularly inspect your face shield to ensure it remains in optimal condition for consistent performance.
- Replace Parts: Replace worn-out straps, visors, or filters as needed.
Proper care ensures reliable performance of your equipment and helps maintain compliance with safety standards. Consider adding specific examples of tools or products for cleaning and maintenance.
Where to Buy Face Shields for Welding
For a wide selection of high-quality face shields, visit our dedicated “Face Shields” category. Whether you need advanced auto-darkening options or durable polycarbonate models, you’ll find the perfect fit.
Include customer reviews or a brief overview of best-selling models to guide purchasing decisions.
Conclusion
We hope this guide has been helpful in navigating the essential factors for choosing the best welding face shield, from material durability to safety standards. Whether you’re working in construction, fabrication, or any other welding-related field, we’re here to support your safety and comfort.
For more guidance, check out our sibling articles like “How To Choose Safety Glasses – A Buyer’s Guide” or explore our main guide on face shields.
Have questions or need advice on selecting the perfect shield? Don’t hesitate to reach out—we’re always here to help ensure your safety and confidence in every purchase.
– The Droppe Team
Frequently Asked Questions
While some shields are versatile, it’s best to choose one based on the specific type of welding you’re doing (e.g., MIG, TIG, arc). Different welding methods require different shade levels for optimal protection.
Replace your shield if it shows signs of damage, such as cracks, scratches, or warping. Regularly inspect it for wear, and replace it every 1-2 years for best performance.
Yes, consider wearing safety glasses under your face shield for extra protection against debris and dust.
Auto-darkening shields are great for most welders, as they adjust the shade based on the arc’s intensity, reducing the need for manual adjustments.
Yes, many face shields are designed to fit comfortably over prescription glasses, but check the model’s specifications to ensure a proper fit.