Choosing the right safety vest can be confusing with different classes—Class 1, Class 2, and Class 3—each designed for specific work environments. By the end of this article, you’ll understand the key differences and know exactly which vest suits your needs.
We’ll guide you through each class, helping you choose the best option based on your work conditions, visibility needs, and compliance with safety standards. Plus, we’ll share tips on maintaining your vest for long-lasting performance.
With this guide, you’ll find the right safety vest and be ready for any situation, ensuring you stay protected and visible on the job. For a broader understanding of selecting safety vests, start with our main article on safety vests.
What Are Safety Vest Classes?
Safety vests are categorized into three classes based on their level of visibility and protection. These classifications empower workers to perform tasks with confidence and ensure maximum visibility in various environments. These classifications are defined by standards like EN ISO 20471, which regulate reflective material, background fabric, and design. The right class depends on the type of work, the environment, and proximity to traffic or heavy machinery.
Class 1 Safety Vests
Best for low-risk environments: Class 1 safety vests offer minimal visibility and are suitable for workers who are away from high-speed traffic or challenging areas. These vests typically:
- Feature fluorescent colors like yellow or orange.
- Include a minimal amount of reflective tape.
- Are used by parking attendants, delivery drivers, and warehouse staff.
Class 2 Safety Vests
Ideal for moderate-risk environments: Class 2 safety vests provide higher visibility, making them suitable for workers near roads with moderate traffic (up to 60 km/h) or in low-light conditions. These vests generally:
- Have more reflective tape than Class 1.
- Include additional design elements for visibility.
- Are commonly used by road construction crews and railway workers.
Class 3 Safety Vests
Essential for high-risk environments: Class 3 vests offer the highest level of visibility, ideal for areas with fast-moving traffic (above 60 km/h) or complex conditions. They:
- Cover more of the body with fluorescent and reflective material.
- Include sleeves with reflective bands for 360-degree visibility.
- Are used by emergency responders, survey crews, and road maintenance workers.
Key Differences at a Glance
This section provides a clear comparison of the safety vest classes, helping you quickly identify the most suitable option for your needs.
A quick comparison can help you decide which class is right for you:
Feature | Class 1 | Class 2 | Class 3 |
Environment | Low risk | Moderate risk | High risk |
Traffic Speed | < 30 km/h | 30-60 km/h | > 60 km/h |
Reflective Material | Minimal | Moderate | Maximum |
Coverage | Torso only | Torso, more reflective tape | Torso, sleeves, full coverage |
Choosing the Right Safety Vest for Your Needs
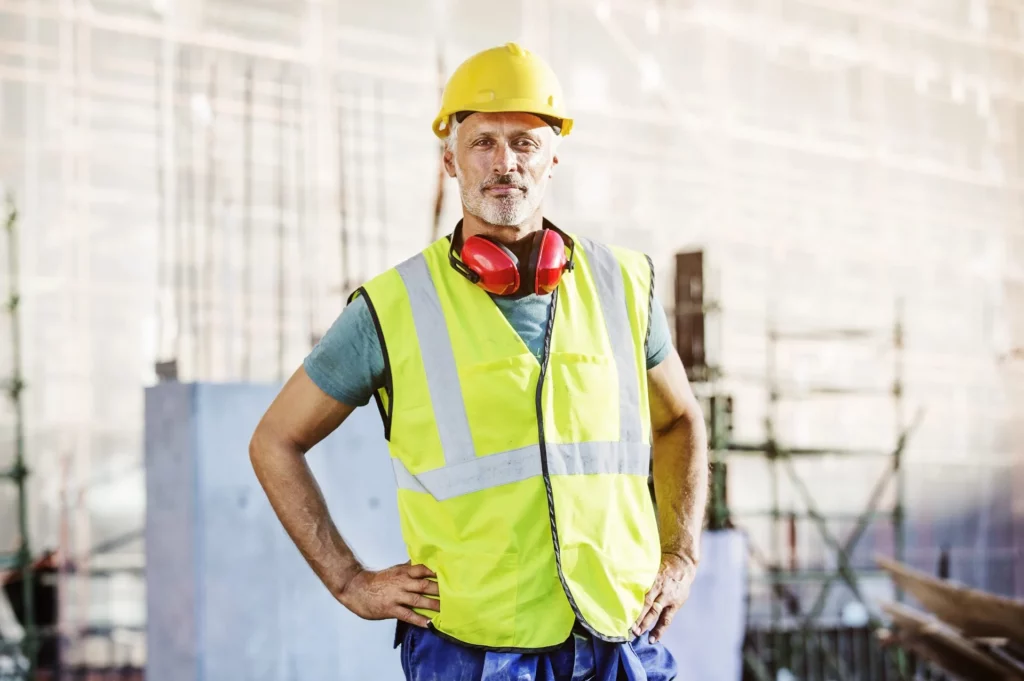
Selecting the correct safety vest requires consideration of your work environment and specific tasks. Below, we outline key factors to guide your decision-making.
Workplace Challenges
Evaluate the traffic conditions in your work environment. A Class 3 vest ensures exceptional visibility and allows you to work confidently in high-speed traffic areas. For indoor tasks with minimal things to consider, a Class 1 vest may suffice.
Regulatory Compliance
Ensure your safety vest complies with EN ISO 20471 standards or other applicable regulations. For detailed insights, refer to Qore Performance’s safety vest classification guide.
Practical Features
Look for features like pockets, zippers, and adjustable sizes that enhance functionality. Our safety vest product category includes a range of options to meet these needs.
Related Products to Enhance Your Safety Gear
Enhancing your safety gear setup with related products ensures comprehensive protection and optimal efficiency, allowing you to focus on your tasks with peace of mind. These items are tailored to meet the demands of various high-risk environments.
In addition to safety vests, consider upgrading your workwear with:
- Hi-vis jackets for extra warmth and visibility.
- Hi-vis pants to ensure complete visibility.
- Hi-vis overalls for all-around coverage.
- Cut-resistant gloves for hand protection.
- Safety shoes to ensure foot safety on the job.
For more buying tips, explore our guides on Hi-vis jackets and Hi-vis pants.
Maintaining Your Safety Vest
Caring for your safety vest ensures it remains effective and reliable over time. Following these steps can help you keep your vest in optimal condition:
To ensure long-lasting performance:
- Clean regularly: Following manufacturer’s washing instructions keeps reflective materials effective and ensures your safety vest maintains its visibility features over time.
- Inspect frequently: Regular inspections ensure your vest maintains its reflective quality and vibrant appearance.
- Replace as needed: Replacing your vest regularly helps maintain optimal safety and confidence during work.
Conclusion
We hope this guide has helped clarify the key factors in selecting the right safety vest, from class distinctions to material and visibility requirements. Whether you’re working near traffic, in construction, or on the road, we’re here to help you make an informed choice for your safety.
Explore our full range of safety vests at Droppe, featuring trusted brands that prioritize quality and visibility. For a deeper dive into selecting the best gear, visit our main guide on safety vests.
Have questions or need assistance in selecting the perfect vest? Don’t hesitate to reach out—we’re always here to ensure your safety and confidence in every purchase.
– The Droppe Team
Frequently Asked Questions
Class 1 vests are suitable for low-risk environments but may not provide adequate visibility in low-light conditions. Consider a Class 2 or Class 3 vest for better visibility.
Yes, many safety vests come with adjustable features like Velcro straps or elastic sides for a customizable fit.
The lifespan of a safety vest depends on usage and care. Regular inspection and proper cleaning can extend its effectiveness.
Class 2 vests are ideal for moderate-risk environments, including construction sites with moderate traffic. For high-risk, fast-moving traffic areas, a Class 3 vest is recommended.
Many safety vests are designed with pockets for added functionality, allowing workers to carry tools or equipment while staying visible.