When working with metal, choosing the right face shield is key to staying comfortable and protected. This guide will help you understand the essential factors—material, protection type, comfort, and compliance with safety standards—so you can find the perfect face shield for your specific tasks.
By the end, you’ll have the confidence to make the best choice for your work environment. Plus, we’ll provide solutions for your next step, whether it’s selecting safety glasses or understanding welding gear.
For a broader overview of choosing face shields, explore the comprehensive How To Choose The Right Face Shields – A Buyer’s Guide.
Key Factors When Choosing a Face Shield for Metal Work
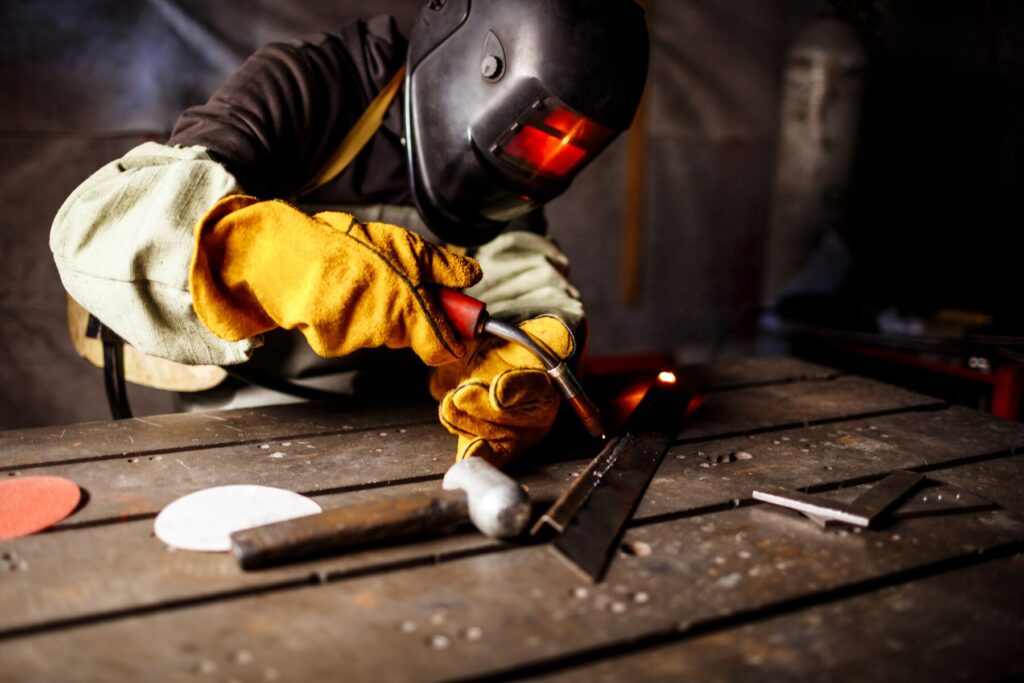
Selecting the right face shield involves evaluating your specific needs, work environment, and the product’s features. Let’s break down the critical considerations.
Material and Lens Properties
The material of the shield determines its durability and protection level. Choosing the right material depends on the specific metalworking task and environment. Common materials include:
- Polycarbonate: Offers excellent impact resistance, making it ideal for metalworking tasks involving flying debris.
- Acetate: Provides chemical resistance, suitable if your metalworking involves oils or solvents.
- Mesh visors: Lightweight but less protective against fine particles and sparks; best for lower-risk tasks.
Choose shields with anti-fogging and scratch-resistant coatings for enhanced visibility and precision during work.
Type of Protection
Choose a shield designed for your specific application:
- Heat-resistant face shields: Essential for welding or tasks involving molten metal.
- Impact-resistant shields: Necessary for grinding or cutting where high-speed debris is common.
- UV and IR protection: Crucial for welding to prevent long-term damage to your sight.
For more insights on welding-specific shields, check out How To Choose The Right Welding Glasses – A Buyer’s Guide.
Standards and Certification
Face shields should meet the robust requirements of European PPE Regulation 2016/425 and relevant EN standards to ensure reliable protection such as the following:
- EN 166: For general eye and face protection.
- EN 175: For welding face shields.
- EN 169: For filters that protect against welding light.
Always check product labels or specifications for these standards to ensure quality and compliance. Learn more about EN Standards from this guide in Wikipedia.
Comfort and Fit
Comfort is essential, especially for prolonged use, as it directly impacts productivity and safety. Consider features like:
- Adjustable headgear: Ensures a snug, secure fit.
- Lightweight design: Reduces fatigue during long shifts.
- Sweatbands or padding: Enhances comfort, particularly in high-temperature environments.
Make sure your face shield integrates seamlessly with other PPE like safety glasses and helmets. For additional protection, explore compatible safety glasses.
Durability and Maintenance
Metalworking environments can be harsh. Choose shields with:
- High resistance to wear and tear.
- Replaceable visors or lenses for cost-effective maintenance.
- Easy-to-clean materials to maintain hygiene.
Comparing Face Shields for Metal Work
Here’s a comparison table summarizing key features:
Feature | Polycarbonate | Acetate | Mesh Visors |
Impact Resistance | High | Medium | Low |
Chemical Resistance | Low | High | Low |
Heat Resistance | High | Medium | Low |
Visibility | Excellent | Good | Moderate |
Weight | Medium | Medium | Low |
Best Practices for Using Face Shields in Metal Work
Proper usage enhances the effectiveness of your face shield. Follow these tips:
- Inspect Before Use: Check for cracks, scratches, or loose fittings.
- Wear Complementary PPE: Combine face shields with safety glasses for optimal protection.
- Clean Regularly: Use mild soap and water to remove debris and maintain clarity.
- Store Safely: Keep shields in a protective case to prevent damage when not in use.
Where to Buy Face Shields for Metal Work
For a curated selection of face shields tailored to metalworking tasks, visit Droppe’s Face Shields Collection. Ensure compatibility with related products, such as safety glasses.
For more detailed buying guides on related categories, explore:
Conclusion
We hope this guide has been helpful in navigating the key factors for selecting the best face shield for metal work, from material durability to industry standards. Whether you’re involved in welding, grinding, or cutting, we’re here to support your safety and comfort.
Explore the full range of face shields on Droppe, featuring trusted brands designed for your specific needs.
For a deeper dive into all things face shields, refer to How To Choose The Right Face Shields – A Buyer’s Guide.
Have questions or need help choosing the right face shield? Feel free to reach out—we’re always here to assist you in making the best choice for your protection and peace of mind.
– The Droppe Team
Frequently Asked Questions
Ensure the shield has adjustable headgear and sits comfortably without obstructing your vision or causing pressure points.
Yes, choose a face shield that is compatible with safety glasses for optimal protection.
Replace the shield if it becomes scratched, cracked, or damaged to maintain clear visibility and protection.
Yes, as long as they remain in good condition. Regular cleaning and maintenance help extend their lifespan.
Polycarbonate is impact-resistant, ideal for debris protection, while acetate offers better chemical resistance for tasks involving solvents.