Welding exposes you to extreme heat, sparks, and sharp materials, making safety a top concern. This comprehensive guide ensures you’ll know exactly how to choose the best leather gloves for welding tailored to your needs, combining expertise on materials, features, and durability.
By the end of this article, you’ll not only be equipped with the knowledge to choose the right gloves but also find solutions for other protective gear challenges to enhance your safety and efficiency.
For a broader understanding of leather work gloves, visit our parent article: Selecting The Best Leather Work Gloves: A Practical Guide.
Types of Leather for Welding Gloves
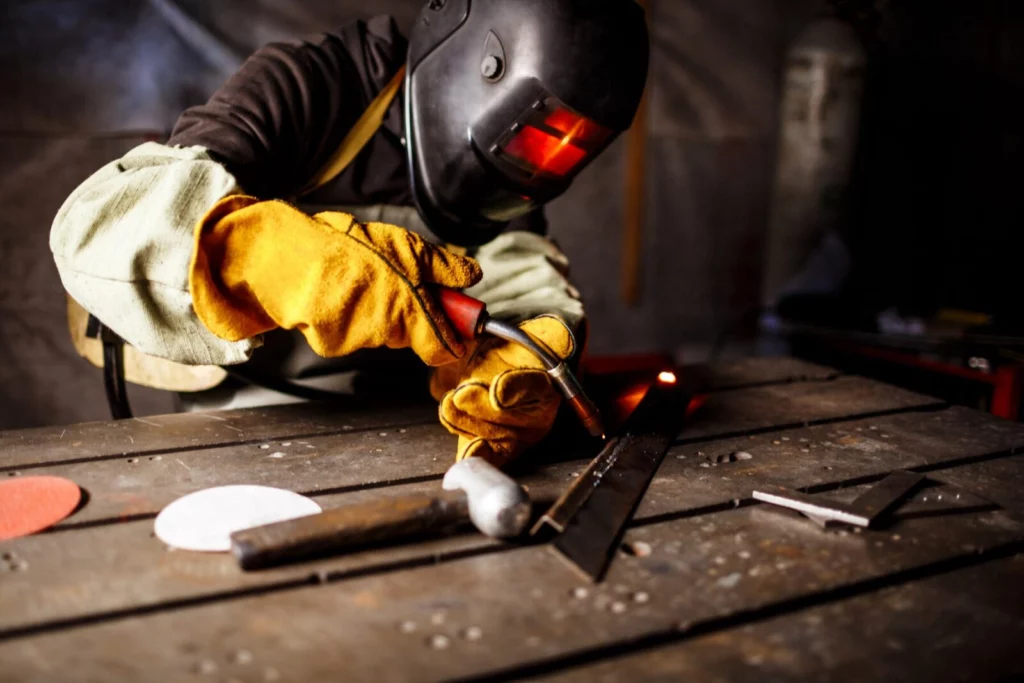
Not all leather is created equal, especially for welding. Understanding the properties of various leather types helps in making the right choice:
- Cowhide: Durable, heat-resistant, and abrasion-resistant, making it ideal for stick welding.
- Pigskin: Soft, flexible, and highly resistant to oil and moisture, suitable for TIG welding.
- Goatskin: Lightweight and pliable, offering excellent dexterity for intricate tasks.
- Deerskin: Soft and comfortable, often chosen for light welding tasks requiring flexibility.
For more on leather glove materials, explore our Leather Work Gloves Buying Guide.
Leather Type | Key Features | Best Use Cases |
Cowhide | Tough, heat-resistant, durable | Stick Welding |
Pigskin | Oil/moisture-resistant, flexible | TIG Welding |
Goatskin | Lightweight, excellent dexterity | TIG Welding |
Deerskin | Soft, comfortable, good flexibility | Light Welding |
Key Features to Look For
To ensure safety and performance, welding gloves must meet specific criteria:
- Heat Resistance: Look for gloves that protect against high temperatures, especially in MIG and stick welding.
- Dexterity: Essential for TIG welding, where precision matters most.
- Durability: Reinforced stitching and abrasion-resistant materials extend glove life.
- Cuff Length: Longer cuffs protect your wrists and forearms from sparks and heat.
- Lining: Cotton or Kevlar linings add insulation and comfort.
Ensure the gloves you choose comply with relevant European standards like EN 407, which evaluates thermal risks such as resistance to heat, flames, and molten metal splashes, ensuring your gloves provide comprehensive protection during welding tasks. Learn more about these standards from this resource in wikipedia.
Welding Glove Recommendations by Welding Type
Different welding techniques demand different glove properties. For example, TIG welding involves precise, detailed work where gloves must ensure fine motor control perfect for tasks like delicate metal joining.
MIG welding, in contrast, deals with higher heat and sparks, so gloves designed for this method prioritize heat resistance and durability.
Stick welding, often used for industrial jobs, requires the toughest gloves to handle intense heat and protect against heavy sparks. Here’s a breakdown:
TIG Welding
TIG welding requires precision and finesse. Gloves must offer high dexterity without compromising protection.
- Recommended Material: Goatskin or pigskin.
- Features: Thin leather, snug fit, heat resistance.
- Example Product: Lightweight goatskin gloves with Kevlar stitching.
MIG Welding
MIG welding involves more heat and sparks, requiring robust protection.
- Recommended Material: Cowhide or pigskin.
- Features: Medium thickness, reinforced palms, heat-resistant lining.
- Example Product: Split cowhide gloves with a cotton lining.
Stick Welding
Stick welding requires gloves with exceptional durability to withstand the intense heat and sparks, ensuring your hands remain protected throughout the process.
- Recommended Material: Cowhide.
- Features: Thick leather, long cuffs, heavy-duty lining.
- Example Product: Thick cowhide gloves with extended gauntlets.
For a variety of options, check out our Leather Work Gloves category.
Sizing and Fit: A Practical Guide
Proper glove fit ensures comfort and safety. Use this guide to find your size:
- Measure the circumference of your palm in centimeters.
- Compare the measurement with the manufacturer’s sizing chart.
Hand Circumference (cm) | Size |
18–20 | Small |
21–22 | Medium |
23–25 | Large |
26–27 | X-Large |
A snug fit prevents slipping and enhances dexterity. A snug fit enhances safety and performance, especially during intricate tasks, by preventing slipping and improving precision.
Caring for Your Leather Welding Gloves
Proper maintenance extends the life of your gloves and ensures optimal performance:
- Cleaning: Use a damp cloth to remove debris. Avoid soaking leather.
- Storage: Store gloves in a dry, cool place to maintain their flexibility and extend their lifespan.
- Conditioning: Apply leather conditioner periodically to maintain flexibility.
For more on maintaining work gloves, visit our related guide: How To Clean Leather Work Gloves.
Complementary Gear for Welders
Pair your gloves with high-quality protective gear for full safety:
- Work Jackets: Protect your upper body from heat and sparks. Explore options from our collection.
- Work Pants: Reinforced pants shield your legs during welding tasks. See our selection.
- Cut-Resistant Gloves: For tasks requiring sharp tool handling. Learn more from our selection.
Related Guides for Further Reading
If you’re interested in exploring related glove types and uses, check out these helpful resources:
- How To Choose Cut-Resistant Gloves – A Buyer’s Guide
- How To Choose The Right Work Gloves – A Buyer’s Guide
- How To Choose The Right Impact-Resistant Gloves: A Buyer’s Guide
Conclusion
We hope this guide has provided clarity on the essential factors for selecting the best leather gloves for welding, from material types to specific features for each welding method. Whether you’re ensuring safety during TIG welding or seeking robust protection for stick welding, we’ve got you covered. Explore the wide range of gloves and protective gear at Droppe to find trusted brands that meet your needs.
Still unsure or need tailored advice? Our team is here to help with expert guidance for your next purchase—ensuring not just safety but confidence in every welding task. And when you’re ready to gear up further, we’ll also assist in selecting complementary protective gear to complete your setup.
– The Droppe Team
Frequently Asked Questions (FAQ)
Yes, welding gloves made of durable leather, like cowhide or pigskin, can be used for tasks requiring heat resistance, abrasion protection, or handling sharp materials. However, ensure the gloves meet the specific safety standards for the task, such as EN 388 for mechanical risks.
Lined gloves provide added insulation and comfort, making them suitable for high-heat applications like stick welding. Unlined gloves, on the other hand, are thinner and offer greater dexterity, which is essential for TIG welding and more precise tasks.
Replace your gloves if you notice significant wear, such as thinning leather, holes, or compromised stitching. Additionally, if the gloves lose their heat resistance or no longer fit securely, they should be replaced to ensure safety and effectiveness.
Most welding gloves are not waterproof or chemically resistant. Pigskin gloves offer some moisture resistance, but for tasks involving chemicals or water, opt for specialized chemical-resistant gloves instead.
While most welding gloves come in standard sizes, some manufacturers offer customization options for fit, materials, or features like reinforced palms. Alternatively, you can use glove liners or add-ons to enhance comfort or protection. Always ensure modifications don’t compromise safety standards.