Grinding and cutting tasks require effective protection for your face and eyes. With so many options available, selecting the right face shield can feel tricky. But don’t worry—by the end of this guide, you’ll know exactly what to look for and how to make the best choice for your needs. We’ll cover essential features, safety standards, and how to pair your shield with other protective gear for complete safety.
Our guide includes practical tips on durability, comfort, and visibility, tailored specifically for these tasks. You’ll also learn how to maintain your shield and find complementary protective gear to ensure comprehensive safety.
Once you’ve chosen the right shield, we’ll help you maintain it and guide you through picking the next piece of gear you may need. Let us make your safety setup simple and effective.
This article is a detailed companion to “How to Choose the Right Face Shields – A Buyer’s Guide”, offering targeted advice for grinding and cutting applications.
Key Features to Look For in Grinding and Cutting Face Shields
Choosing the right face shield involves considering specific features that cater to the demands of grinding and cutting. These include:
Material Durability
Select face shields made from durable and reliable materials like polycarbonate or acetate. Polycarbonate offers superior impact resistance, while acetate provides excellent chemical resistance and clarity.
Adjustable Fit
A secure and adjustable headband ensures the face shield stays in place during strenuous tasks. Look for models with ratchet suspension systems for easy customization.
Anti-Fog and Scratch Resistance
Clear visibility is crucial. Opt for shields with anti-fog coatings to maintain clarity in humid conditions and scratch-resistant surfaces for longevity.
Compliance with Safety Standards
Ensure the face shield meets European safety standards, such as EN 166:2001, which specifies requirements for personal eye protection against ensuring robust protection during various tasks. This ensures reliable and effective protection tailored to your needs. Learn more about European standards here.
Comparing Face Shields for Grinding and Cutting
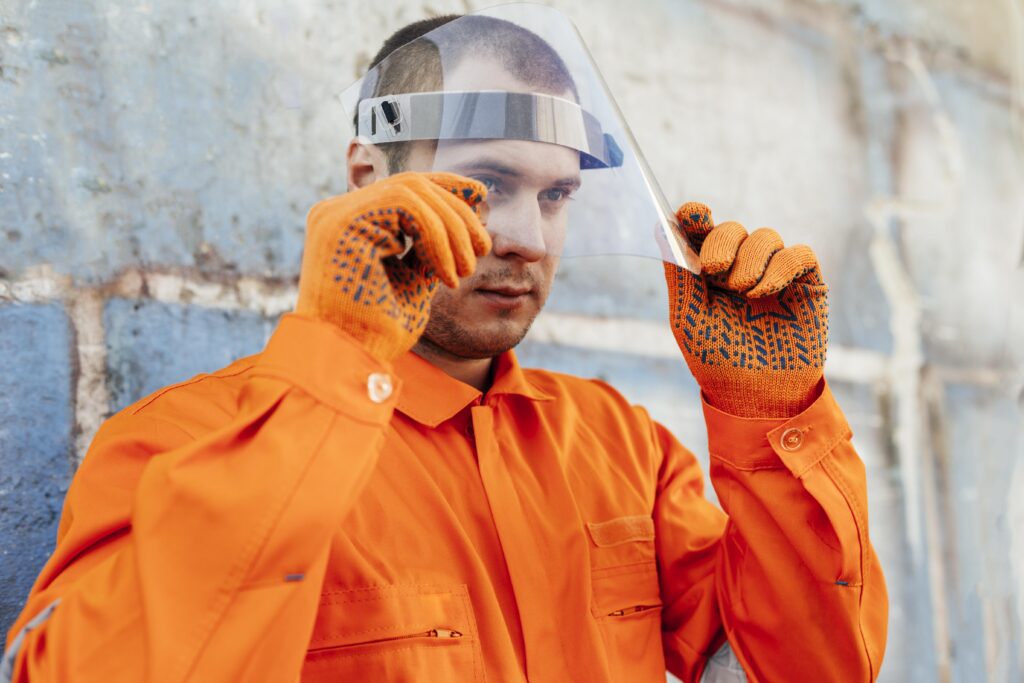
Feature | Grinding | Cutting |
Material Preference | Polycarbonate (impact resistance) | Polycarbonate or Acetate (clarity and chemical resistance) |
Shield Coverage | Full face, extended sides | Full face |
Coatings Needed | Anti-fog, scratch-resistant | Anti-fog, UV-resistant |
Weight Consideration | Lightweight | Lightweight |
Proper Usage and Maintenance Tips
To maximize the effectiveness of your face shield:
- Inspect before use: Keep your face shield in top condition by regularly inspecting for any signs of wear to keep your face shield performing at its best.
- Clean regularly: Use a mild soap solution and a soft cloth to clean the shield. Avoid harsh chemicals that may damage coatings.
- Store safely: Keep in a protective bag or case to prevent scratches.
Pairing with Other PPE
For comprehensive protection, combine your face shield with other PPE. For example:
- Safety Glasses: Enhance protection against fine particles. Explore safety glasses here.
- Hearing Protection: Using earmuffs or earplugs ensures a quieter and more focused working environment during grinding and cutting tasks. Choose earmuffs or earplugs that comply with EN 352 standards.
- Respirators: Maintain cleaner air quality and breathe more comfortably with respirators designed for dust and fume filtration. Look for models meeting EN 149 standards.
Related Articles for Further Reading
- How to Choose Safety Glasses – A Buyer’s Guide
- How to Choose the Right Welding Glasses – A Buyer’s Guide
- Welding Helmets: Everything You Need to Know
Conclusion
We hope this guide has provided you with valuable insights into selecting the right face shield for grinding and cutting tasks. From material durability to essential safety standards, we’ve covered the key factors to ensure you choose the best protection for your needs. Whether you’re working in a workshop, construction site, or any environment involving grinding or cutting, we’re here to support you.
Find a wide selection of high-quality face shields tailored for grinding and cutting at Droppe’s Face Shields Category.
Use the filtering options to easily locate products specifically designed for your needs. For additional options, explore safety glasses to complement your purchase.
Have questions or need help choosing the perfect face shield? Feel free to reach out—we’re always here to help ensure your safety and confidence with every purchase.
– The Droppe Team
Frequently Asked Questions
Yes, polycarbonate face shields work well for both tasks, but for cutting, you may want to consider additional UV protection.
Yes, face shields provide full-face protection, which safety glasses alone cannot offer, especially against flying debris and sparks.
Use a mild soap solution and a soft cloth to clean it. Avoid harsh chemicals that could damage the coatings.
Store your shield in a protective bag or case to prevent scratches and damage when not in use.
Replace your face shield if it shows signs of damage, such as cracks or deep scratches, or if it no longer provides clear visibility.