If you’re working with electrical equipment, choosing the right hard hat is key to ensuring safety and compliance. This guide provides all the information you need to select the perfect hard hat for electrical work, including key standards, materials, and features. As experts in safety gear, we’ll offer clear insights to help you make the best choice. Additionally, we’ll show you how to maintain and fit your hard hat for optimal comfort and performance. Keep reading for everything you need to stay safe and prepared.
For a broader understanding of protective headgear, check out our main article on hard hats and safety helmets, which covers general selection tips and industry standards.
Key Standards for Hard Hats in Electrical Work
Choosing a hard hat involves understanding applicable safety standards. Here are the primary classifications you need to know:
Standard | Region | Key Features |
EN 50365 | Europe | Insulates against voltages up to 1000V AC or 1500V DC. |
IEC 61482-1-2 | Europe | Protects against arc flashes in low and high-voltage environments. |
ANSI Z89.1 Class E | International | Resists up to 20,000 volts; often used as a reference for high-voltage work. |
Ensure that the hard hat you choose complies with EN 50365 for safe use in European electrical workplaces. Learn more about EN Standards from this guide in Wikipedia.
Recognizing Safety Certifications and Avoiding Counterfeit Equipment
When selecting a hard hat, it’s vital to ensure that the product meets recognized safety standards and is not counterfeit. Here are tips to verify compliance:
- Look for Certification Labels: Check for labels or markings indicating compliance with EN 50365, IEC 61482-1-2, or other relevant standards. Genuine products will include clear, legible labels often embossed on the hard hat.
- Verify Manufacturer Authenticity: Purchase from reputable suppliers or directly from manufacturers known for safety gear. Choose trusted brands with clear documentation to guarantee reliable performance and compliance.
- Check for Documentation: Authentic hard hats are often accompanied by a certificate of compliance or a user manual that outlines testing standards and specifications.
- Inspect the Build Quality: Authentic helmets ensure high-quality materials and consistent finishes, providing reliable safety for electrical work. Ensure the product feels durable and aligns with industry expectations.
For more insights into hard hat classifications and types, refer to our in-depth guide.
Material and Construction Considerations
Hard hats designed for electrical work are made from non-conductive materials like polycarbonate or high-density polyethylene (HDPE). These materials provide:
- Electrical insulation to prevent conduction.
- Impact resistance for protection against falling objects.
- Durability to perform effectively across various challenging environments.
Always opt for hard hats labeled as Class E (Electrical) or meeting EN 50365 standards for maximum protection.
Types of Hard Hats for Electrical Work
Understanding the different types of hard hats helps ensure you select the right one for your job. Here are the primary options:
Class E Hard Hats
Designed for high-voltage environments, these hard hats can withstand up to 20,000 volts of electrical exposure. They are commonly used in utility work and industrial maintenance.
Class G Hard Hats
While not as robust as Class E, Class G hard hats provide low-voltage protection (up to 2,200 volts) and are suitable for light electrical work in construction or repair settings.
EN 50365-Certified Helmets
These helmets are specific to Europe and cater to electrical insulation requirements for low-voltage environments, ideal for professionals working on live circuits.
Workplace Scenarios and Best Practices
Understanding where and how specific hard hats are used can guide your choice:
- High-Voltage Power Line Maintenance: Equip yourself with Class E hard hats for confidence and safety when working around high-voltage systems and challenging conditions. These provide reliable safety for utility workers working on live power lines.
- Industrial Machinery Repair: For environments with low-voltage exposure, Class G hard hats are suitable. Maintenance workers operating around control panels or machinery benefit from their lighter construction.
- Construction Sites with Live Wires: When live electrical wiring is present, EN 50365-certified helmets are an excellent choice. They ensure compliance with European standards while offering adequate insulation.
These scenarios emphasize how the right hard hat can protect you effectively based on your specific job requirements.
Features to Look for When Choosing a Hard Hat
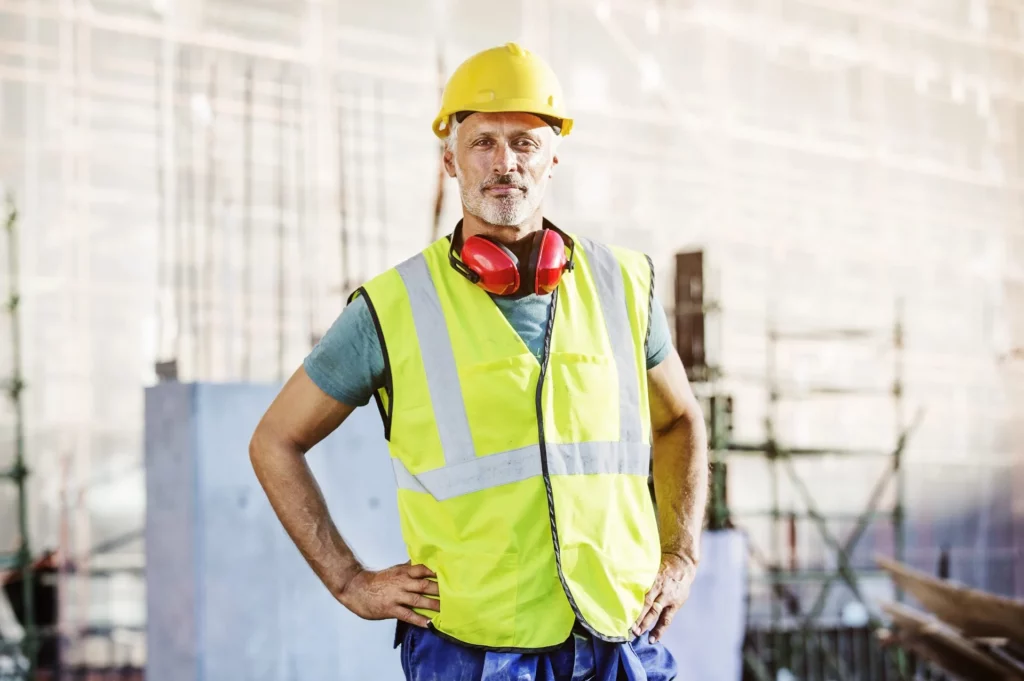
To select the best hard hat for electrical work, evaluate these features:
1. Insulation
Ensure the hard hat is made of non-conductive materials and complies with the EN 50365 or Class E standards.
2. Comfort
Look for features like adjustable suspension systems and padded straps to reduce fatigue during long work hours.
3. Ventilation
While insulation is critical, many hard hats feature ventilation slots for added comfort. Ensure these slots do not compromise electrical safety.
4. Chin Straps
For secure fitting, especially in windy or dynamic environments, opt for a hard hat with a durable chin strap.
5. Accessories
Some hard hats support attachments like headlamps or ear defenders, enhancing utility without compromising safety. For guidance on headlamps, explore our headlamp buying guide.
How to Maintain Your Hard Hat
Proper maintenance extends the lifespan of your hard hat and ensures ongoing safety:
- Regular inspections help ensure your hard hat remains in peak condition for ongoing protection.
- Clean with mild soap and avoid abrasive chemicals that could degrade materials.
- Replace every 2-5 years or sooner after any notable impact to ensure continuous protection.
Where to Buy Hard Hats for Electrical Work
Find high-quality hard hats and safety helmets in our Hard Hats and Safety Helmets product category. Our range includes certified options suitable for electrical work.
Additionally, explore related products to enhance your workplace safety:
Tips for Selecting the Right Hard Hat Size
Getting the correct fit is essential for comfort and safety. Follow these steps:
- Measure your head circumference using a tape measure in centimeters.
- Refer to size charts provided by manufacturers.
- Adjust the suspension system for a snug fit without pressure points.
Conclusion
We hope this guide has been helpful in navigating the essential factors for choosing the best hard hat for electrical work, from material selection to industry standards. Whether you’re working on high-voltage projects or handling low-voltage tasks, we’re here to support your safety needs.
Explore the full range of hard hats and safety helmets on Droppe, where trusted brands are just a click away.
To explore additional guides and insights, check out our complete collection of articles on safety equipment.
Have questions or need advice on selecting the perfect hard hat? Don’t hesitate to reach out—we’re always here to help ensure your safety and confidence with every purchase.
– The Droppe Team
Frequently Asked Questions
Most hard hats last 3-5 years, depending on material and usage. Always check manufacturer recommendations.
No, replace any hard hat showing cracks or damage to maintain safety.
Type 1 provides vertical impact protection, while Type 2 offers both vertical and lateral protection.
Yes, most hard hats come with adjustable suspension systems for a customized fit.
For minimal hazards, bump caps or lighter helmets may suffice, but check your workplace requirements.